Unusual corner connection of a profile pipe
Throughout my life I have come across many connections of profile pipes. At different angles or bevels, with and without stops, with inserts and simple joints. But it struck me with the simplicity and originality of the approach. That very case when everything ingenious is mind-blowingly simple!
Today we will talk about a connection at an angle of 90 degrees, in which the outer edge of the joint is rounded to the correct radius. Of course, such a connection is unusual, and you are unlikely to see it at every step. But it’s still worth paying attention to it. And now you will see this for yourself.
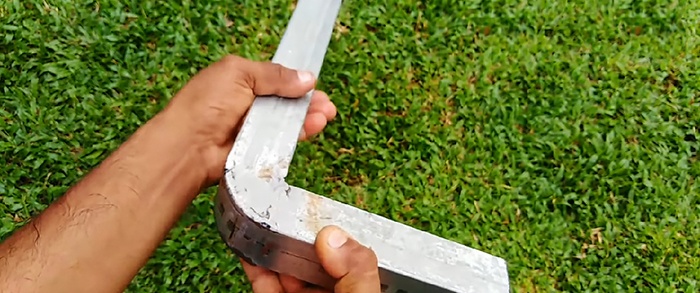
For the experiment, you can take an unnecessary piece of square pipe with a cross-section, for example, 40x40 mm. Select a length of no more than a meter so that it is convenient to work with the cutout of the joint on the pipe with a grinder. By the way, this method does not exactly involve a connection, since it was originally designed to be made from one pipe, bent at a right angle.
We start by marking the cutout with a marker.In the middle of the pipe, using a square, mark a circular line along all its walls. It will be basic. We measure 2 cm from it and repeat the marking.
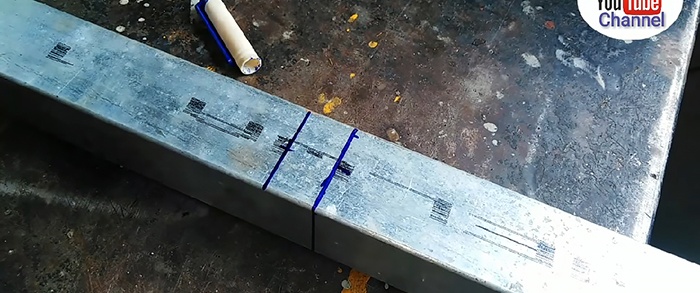
To draw arc lines for bending, you can take a grinder cutting wheel, or use a suitable circle. The distance between the extreme point of the arc and the nearest line should be about 3 cm. We make markings on opposite walls of the pipe in the same direction of the lines.
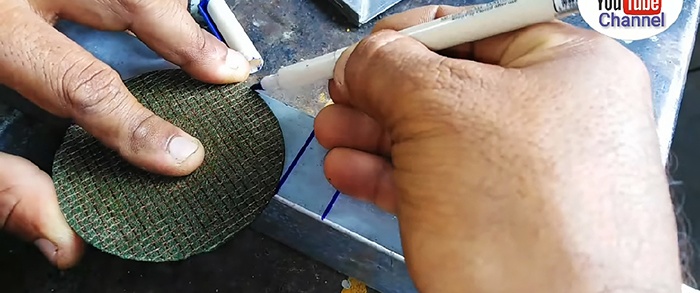
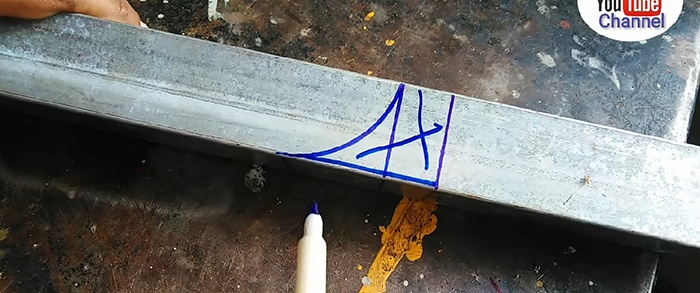
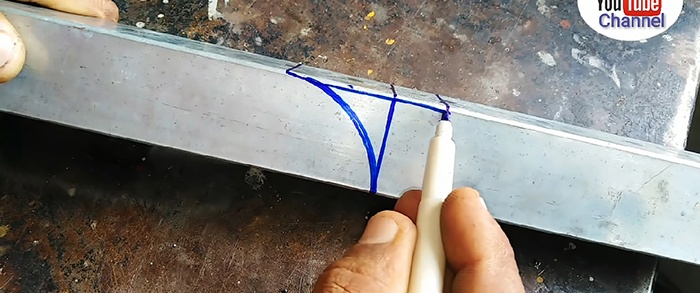
The extreme points of the arcs must be connected to the top of the base line. This way we will get a clear and correctly calculated cutting line for the joint.
The cutting itself can be made with a small grinder and a disk with a diameter of 125 or 115 mm. The smaller the disc circumference, the more accurate the cutting of arc lines will be.
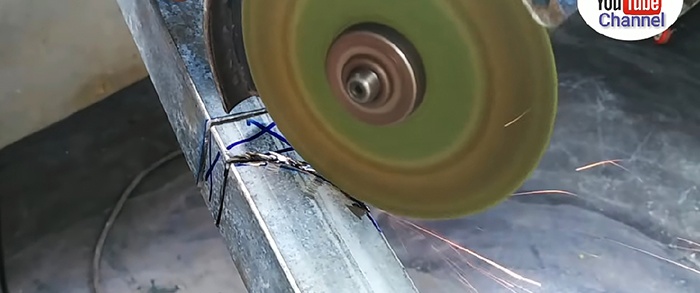
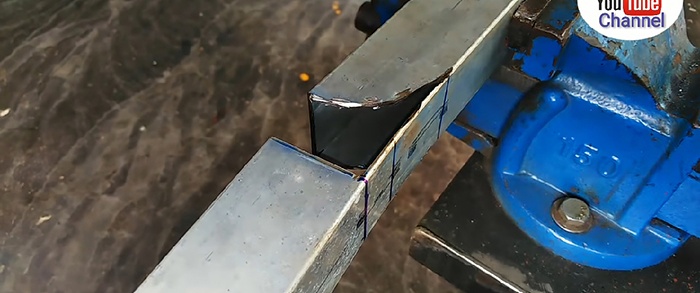
Having finished cutting the joint, we bend the part of the pipe cut along straight lines to the position of a right angle. The resulting outer joint wall will take the form of cut arc lines.
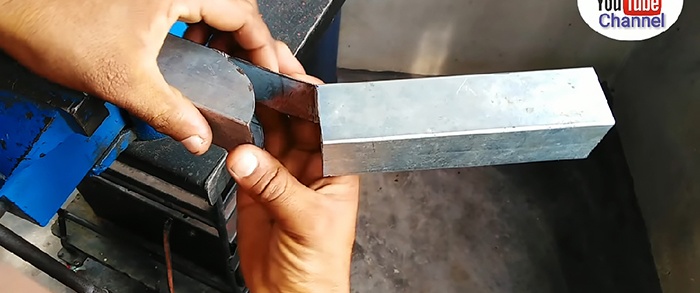
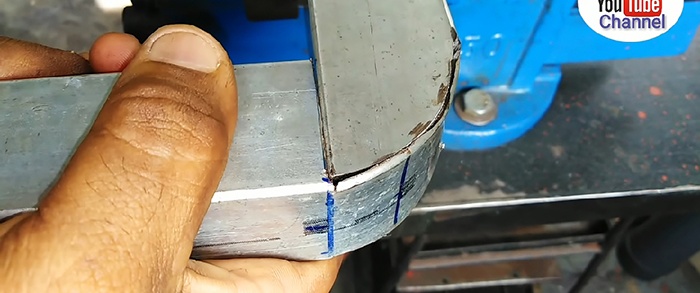
For greater connection accuracy, place a square on the inside of it and secure the connection by hand. Now you can start welding.
We grab the pipe pointwise at the point where it opens with the electrode. Next, we weld all the joints with continuous seams without breaks.
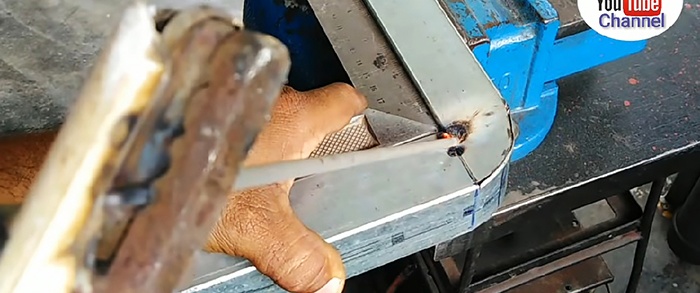
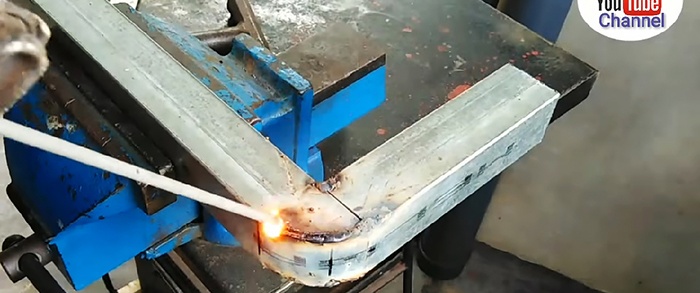
After removing the scale, we clean all the joints with a grinding wheel on a grinder.
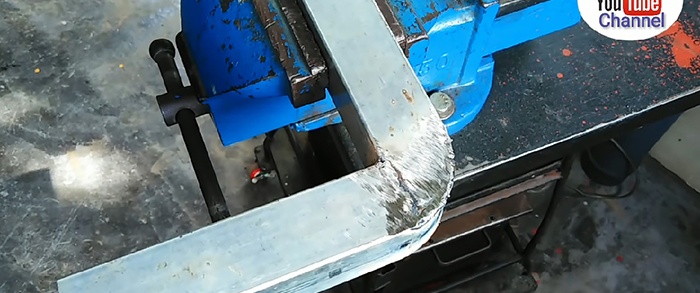
Try making such a corner joint with your own hands and see how simple and elegant it is.
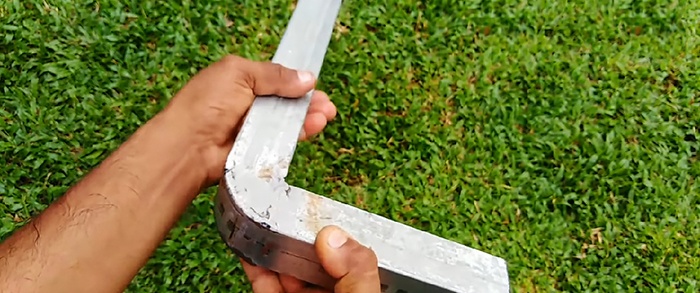
Today we will talk about a connection at an angle of 90 degrees, in which the outer edge of the joint is rounded to the correct radius. Of course, such a connection is unusual, and you are unlikely to see it at every step. But it’s still worth paying attention to it. And now you will see this for yourself.
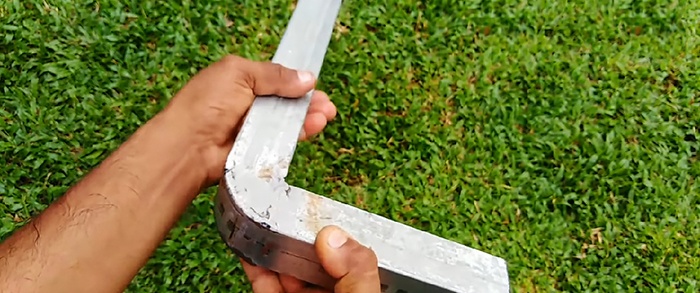
For the experiment, you can take an unnecessary piece of square pipe with a cross-section, for example, 40x40 mm. Select a length of no more than a meter so that it is convenient to work with the cutout of the joint on the pipe with a grinder. By the way, this method does not exactly involve a connection, since it was originally designed to be made from one pipe, bent at a right angle.
You will need the most common tool for working with metal:
- Grinder (angle grinder) with cutting and grinding discs;
- Welding machine;
- Vise;
- Hammer;
- Construction square;
- Marker for marking lines.
Manufacturing technology
We start by marking the cutout with a marker.In the middle of the pipe, using a square, mark a circular line along all its walls. It will be basic. We measure 2 cm from it and repeat the marking.
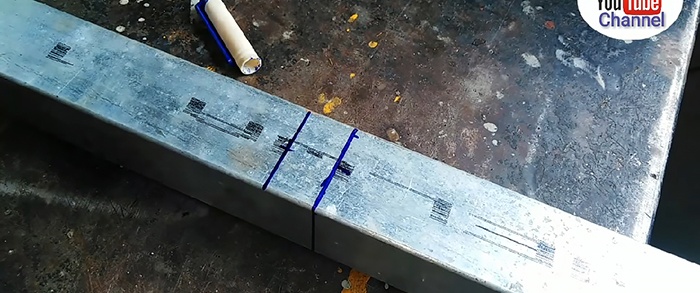
To draw arc lines for bending, you can take a grinder cutting wheel, or use a suitable circle. The distance between the extreme point of the arc and the nearest line should be about 3 cm. We make markings on opposite walls of the pipe in the same direction of the lines.
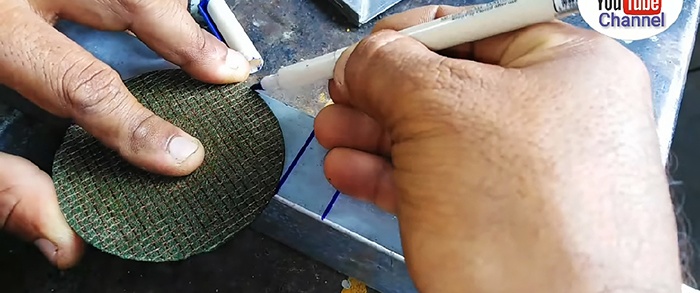
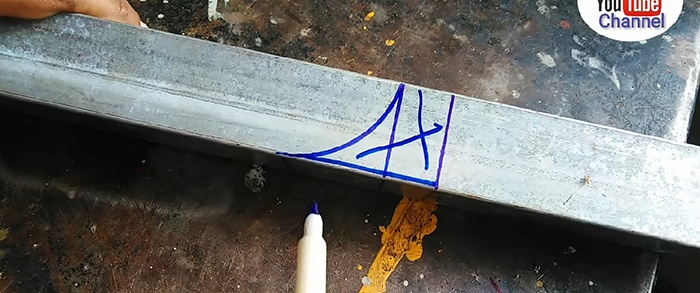
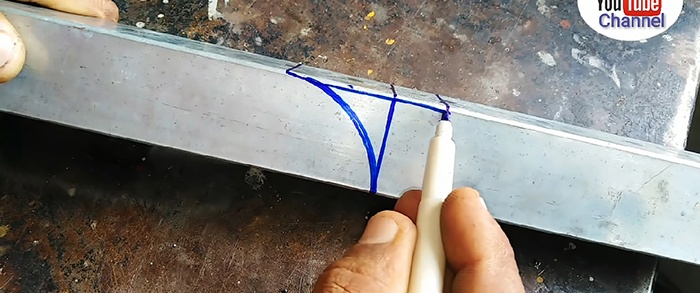
The extreme points of the arcs must be connected to the top of the base line. This way we will get a clear and correctly calculated cutting line for the joint.
The cutting itself can be made with a small grinder and a disk with a diameter of 125 or 115 mm. The smaller the disc circumference, the more accurate the cutting of arc lines will be.
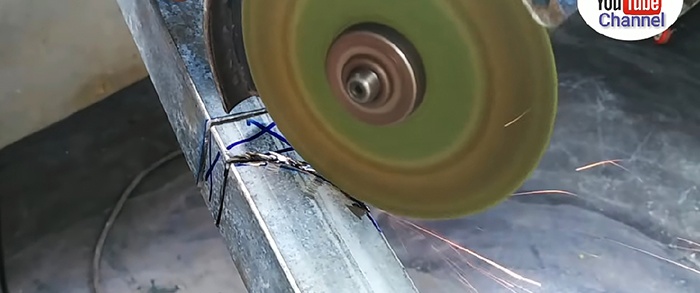
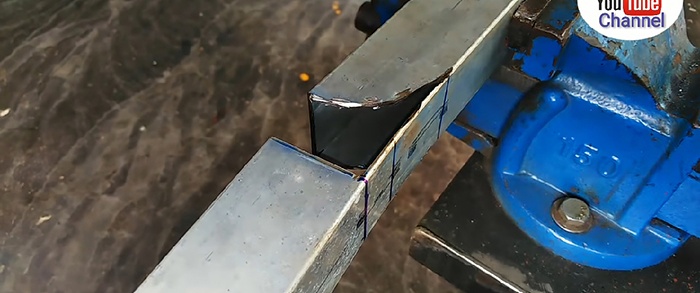
Having finished cutting the joint, we bend the part of the pipe cut along straight lines to the position of a right angle. The resulting outer joint wall will take the form of cut arc lines.
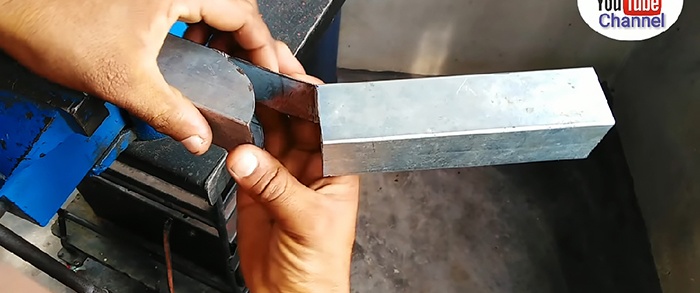
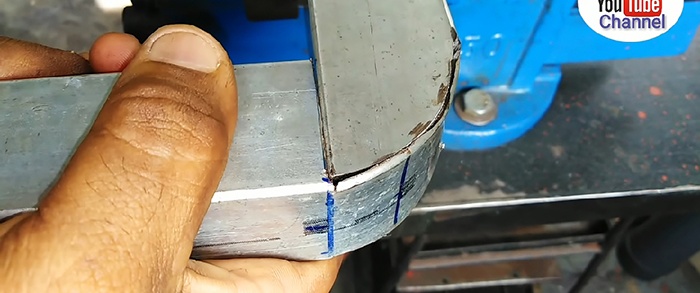
For greater connection accuracy, place a square on the inside of it and secure the connection by hand. Now you can start welding.
We grab the pipe pointwise at the point where it opens with the electrode. Next, we weld all the joints with continuous seams without breaks.
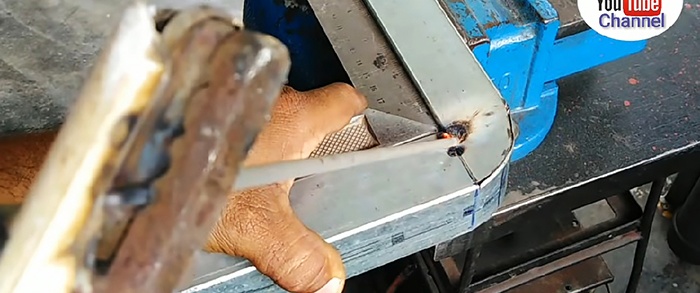
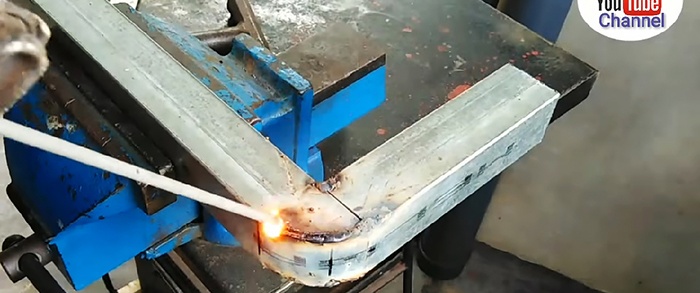
After removing the scale, we clean all the joints with a grinding wheel on a grinder.
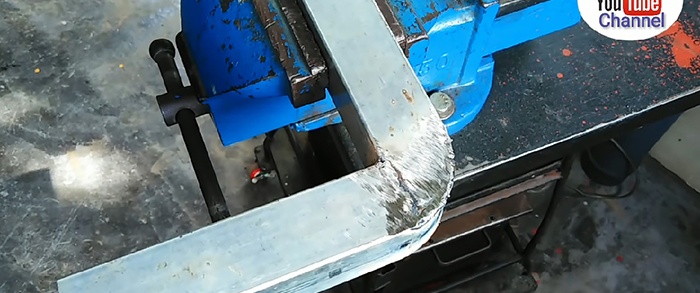
Try making such a corner joint with your own hands and see how simple and elegant it is.
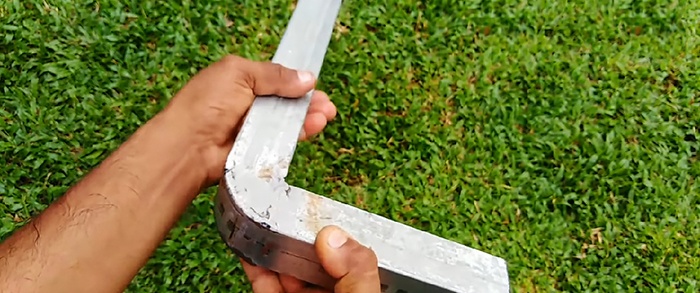
Watch the video
Similar master classes
Particularly interesting
Comments (0)