How to make a cross-cutting machine from an old bicycle and an angle grinder
Outdated mechanisms can be used to make other useful tools and devices. This will rid the site of accumulated scrap metal, and will also allow you to abandon the purchase of factory solutions.
A miter saw is used to cut long rolled metal in large quantities at specified angles. In order not to buy it, you can make a stand for an angle grinder and perform all the same steps, but saving a considerable amount.
The bicycle steering column, parts of the handlebar, front fork and frame will be used as the rotation mechanism of the rack. The parts are cut out, then a strip with drilled holes is welded to the fork for installing an angle grinder.
Next, the cut out part of the frame is welded to the sheet steel base.
The fork is inserted into it together and tightened with a nut. After this, the steering wheel trim is installed and tightened securely.
Stops from the corner are screwed onto the base of the stand to position the workpiece when cutting at 45 and 90 degrees. It is also necessary to cut it at the point where the cutting disc of the grinder mounted on the rotary mechanism touches.
To install the return spring, you will need to weld the nuts to the fork and to the sole. After painting, the stud will be screwed into the nut on the fork. A spring will catch on its edge, the bottom of which can be hooked onto the nut on the sole.
After installing the spring, the angle grinder is screwed on.
To do this, use a clamp for the sewer pipe, tightened on its body. Then the angle grinder is bolted to the strip on the fork into the standard hole for the handle and clamp.
A miter saw is used to cut long rolled metal in large quantities at specified angles. In order not to buy it, you can make a stand for an angle grinder and perform all the same steps, but saving a considerable amount.
Materials:
- old bicycle;
- Sheet steel;
- corner;
- M10 pin;
- nuts M10 – 4 pcs.;
- tension spring.
Rack manufacturing process
The bicycle steering column, parts of the handlebar, front fork and frame will be used as the rotation mechanism of the rack. The parts are cut out, then a strip with drilled holes is welded to the fork for installing an angle grinder.
Next, the cut out part of the frame is welded to the sheet steel base.
The fork is inserted into it together and tightened with a nut. After this, the steering wheel trim is installed and tightened securely.
Stops from the corner are screwed onto the base of the stand to position the workpiece when cutting at 45 and 90 degrees. It is also necessary to cut it at the point where the cutting disc of the grinder mounted on the rotary mechanism touches.
To install the return spring, you will need to weld the nuts to the fork and to the sole. After painting, the stud will be screwed into the nut on the fork. A spring will catch on its edge, the bottom of which can be hooked onto the nut on the sole.
After installing the spring, the angle grinder is screwed on.
To do this, use a clamp for the sewer pipe, tightened on its body. Then the angle grinder is bolted to the strip on the fork into the standard hole for the handle and clamp.
Watch the video
Similar master classes

How to make a weeding cultivator using an old bicycle
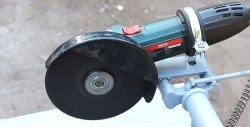
A simple stand for an angle grinder made from a bicycle
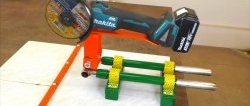
A stand for an angle grinder made from the handle of a children's bicycle. Extremely

DIY trencher made from a brush cutter and a broken grinder
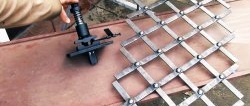
How to make a machine for quickly making forged lattice

How to make a manual potato hiller from an old bicycle
Particularly interesting
Comments (2)