How to Recover Used PP Re-Soldering Fitting
When rewiring polypropylene pipes, the old fittings have to be thrown away, since it is no longer possible to solder them to the new pipe. This is very sad, because American ones, taps and mud pans are not cheap. Using this method, you will be able to repair soldered fittings so that they can be reused.
The soldered fitting must be cut off from the pipe with scissors. The cut is made close to it.
Then you need to cut off the thin edge with solder sagging. Next, use a chamfer remover. It is necessary to expand the inner diameter of the fitting with a soldered tube so that the soldering iron nozzle can fit into it.
After this, a heated soldering iron is inserted into it to melt the circle for installing the crown. This is necessary so that it does not slip off.
After the soldering iron, a crown is inserted into the fitting. Its diameter should be 1 mm less than the outer section of the pipe.With its help you need to drill out the polypropylene in the fitting to the welding depth.
The crown will heat the plastic, so before it hardens, you need to tear out the drilled inner ring from the soldered old pipe with thin-nose pliers. The edge of the fitting is again processed with a bevel remover, and the plastic influx is cut off with a regular mounting knife.
The internal cavity is wiped with a rag in a solvent.
The fitting can then be welded to the new pipe.
Also see how you can make a simple gas soldering iron - https://home.washerhouse.com/en/5723-jelektrichestvo-ne-nuzhno-prostoj-gazovyj-pajalnik-dlja-svarki-polipropilenovyh-trub.html and solder polypropylene pipes anywhere without electricity.
Required tool:
- pipe cutters;
- knife for chamfering pipes;
- screwdriver with crown;
- soldering iron for polypropylene pipes;
- thin-nose pliers.
Repair process for used fittings
The soldered fitting must be cut off from the pipe with scissors. The cut is made close to it.
Then you need to cut off the thin edge with solder sagging. Next, use a chamfer remover. It is necessary to expand the inner diameter of the fitting with a soldered tube so that the soldering iron nozzle can fit into it.
After this, a heated soldering iron is inserted into it to melt the circle for installing the crown. This is necessary so that it does not slip off.
After the soldering iron, a crown is inserted into the fitting. Its diameter should be 1 mm less than the outer section of the pipe.With its help you need to drill out the polypropylene in the fitting to the welding depth.
The crown will heat the plastic, so before it hardens, you need to tear out the drilled inner ring from the soldered old pipe with thin-nose pliers. The edge of the fitting is again processed with a bevel remover, and the plastic influx is cut off with a regular mounting knife.
The internal cavity is wiped with a rag in a solvent.
The fitting can then be welded to the new pipe.
Watch the video
Also see how you can make a simple gas soldering iron - https://home.washerhouse.com/en/5723-jelektrichestvo-ne-nuzhno-prostoj-gazovyj-pajalnik-dlja-svarki-polipropilenovyh-trub.html and solder polypropylene pipes anywhere without electricity.
Similar master classes
Particularly interesting
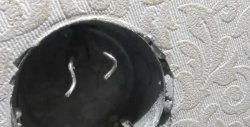
How to install a socket if there are short wires left
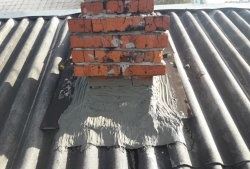
How to eliminate gaps between the chimney and slate
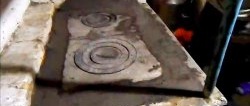
How to mix an ultra-reliable solution for the oven that does not give
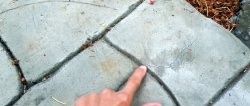
There will be no more cracks: What to add to concrete to make it
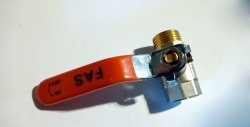
Never buy ball valves without checking with me
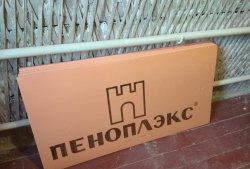
New technology for floor insulation with penoplex
Comments (1)