How to make a threaded dismountable connection of plastic pipes without soldering
PVC or PP pipes are among the best in terms of the balance between cost and reliability, so it makes sense to use them for assembling irrigation systems or animal watering. The only problem is that connecting them involves soldering. The system assembled with a soldering iron does not provide for the possibility of quick disassembly for winter storage, transfer or modernization. For such cases, it is better to carve the pipes yourself. With low water pressure in the system, this is quite safe and very convenient.
What you will need:
- Lighter or burner;
- universal silicone grease;
- PVC or PP pipes 25 mm;
- PVC or PP fittings 25 mm;
- brass fittings 3/4 V, 3/4 N;
- fumlenta.
The process of forming threads on PP pipes
The first step is to cut the pipe into pieces of the required length.
To cut external threads on pipes, you need to clamp any metal fitting with a 3/4 inch female thread in a vice. It must be sprayed with silicone grease.Then we heat the edges of the pipe with a lighter or torch until the plastic begins to melt, and screw it into the fitting.
After 5-10 minutes, the cooled tube is unscrewed. Due to the lubricant, it does not stick to the metal. The result is a strong, dense thread.
The internal thread in plastic fittings is made by screwing a hot brass external thread into it. That is, you need to heat it the other way around. You can also disconnect twisted parts only after the plastic has completely cooled.
Modified pipes and fittings are twisted together with fume tape.
We get a collapsible connection that easily holds the water pressure from the tank. Of course, such pipes cannot be connected to a centralized water supply system (well, unless for a short time, say, to water the garden), but otherwise this is an excellent solution.
Watch the video
Similar master classes
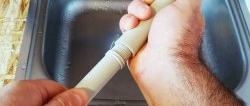
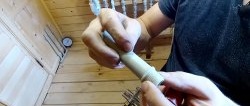
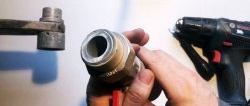
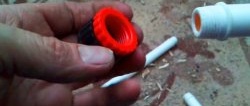
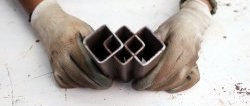
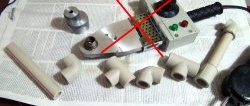
Particularly interesting
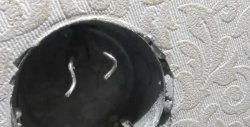
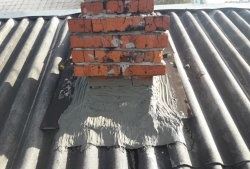
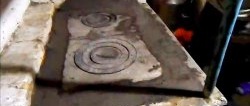
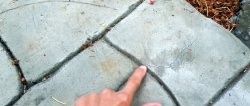
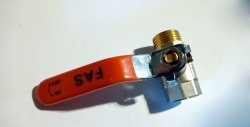
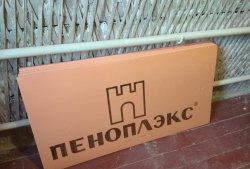