Compresseur d'air d'une unité ZIL et d'un moteur de machine à laver
Les propriétaires de voitures, de motos et de cyclistes doivent souvent gonfler leurs roues ; cette opération manuelle est longue et fastidieuse. Un compresseur d'air vient à la rescousse, qui peut être assemblé à partir d'une unité automobile en état de marche. Un moteur de 300 watts est excellent comme entraînement - ils sont souvent utilisés pour équiper les machines à laver rotatives et automatiques. Examinons en détail le processus de création de l'appareil mentionné.
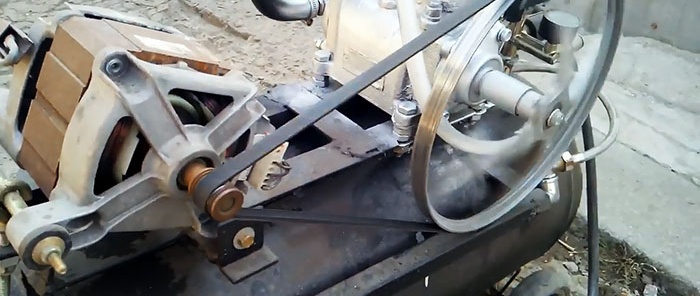
Le processus de fabrication d’un compresseur d’air nécessite des compétences en métallurgie et en plomberie de la part d’un artisan. Pour les travaux, un certain nombre de composants et de pièces ont été nécessaires : neufs ou d'occasion :
Pour effectuer le travail, vous aurez besoin d'un outil de mécanicien, d'une perceuse avec un jeu de perceuses et d'une soudure électrique. Certaines opérations, par exemple l'alésage d'une poulie, sont commandées dans un atelier spécialisé.
La plupart des composants ont été utilisés, nettoyés des contaminants et, si nécessaire, reconstruits. Les principales pièces du compresseur ont été fabriquées dans le garage et assemblées dans l'ordre suivant :
L'unité automobile est montée sur le châssis du récepteur à l'aide de connexions boulonnées.
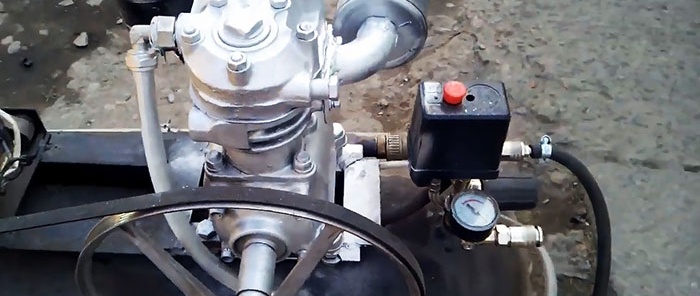
Un entraînement électrique est installé à côté pour que les poulies soient dans le même plan.
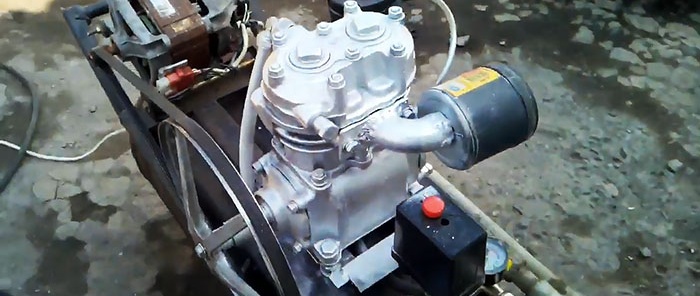
Devant le compresseur sur le châssis, nous montons le système de contrôle automatique et le reconfigurons : mise en marche à une pression de 4 atm, arrêt à 6 atm.
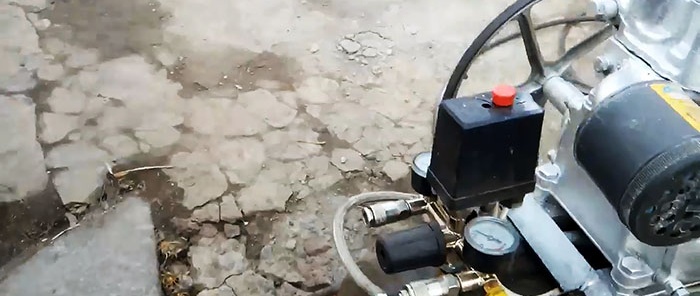
Nous perçons un trou dans le couvercle du carter du compresseur, coupons un filetage et vissons un carré. Nous y attachons un tube avec un réservoir d'huile et, au-dessus, nous découpons un reniflard à travers lequel l'huile sera expulsée dans le réservoir de stockage.
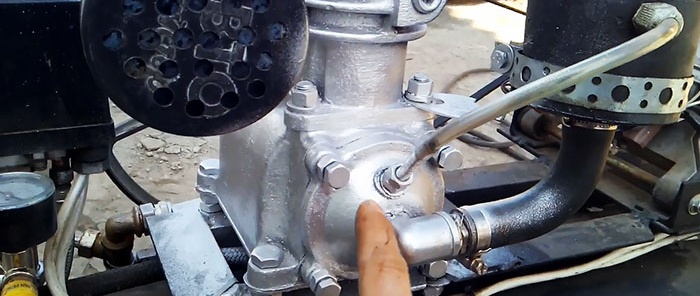
Nous soudons un radiateur de refroidissement à air à partir de tubes en acier, qui sert simultanément de poignée pour le transport. D'un côté, nous y connectons la sortie du compresseur, de l'autre, nous connectons le tube d'alimentation en air au récepteur.
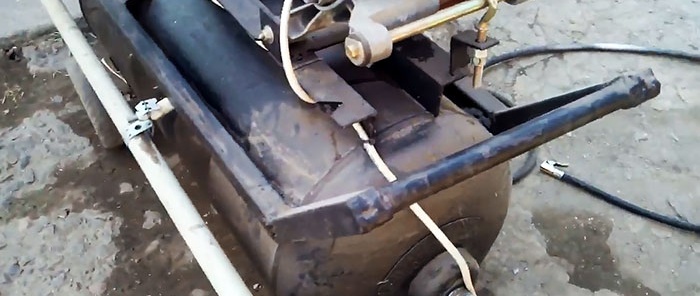
Nous tournons la conduite d'air à l'aide de deux carrés.
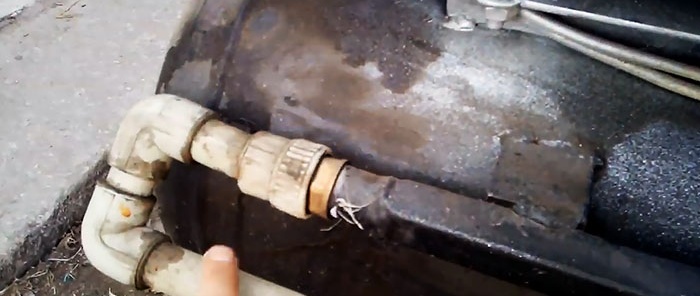
Nous installons un clapet anti-retour à l'entrée du récepteur.
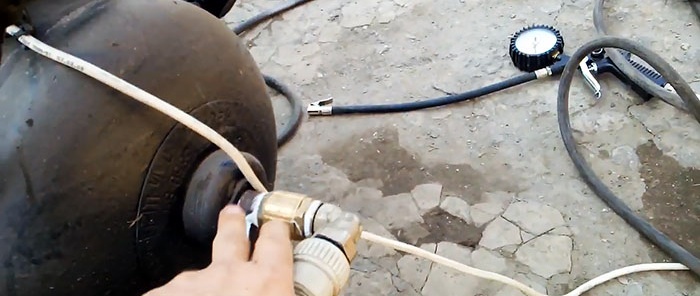
A la sortie du récepteur, installez une vanne et raccordez un tuyau flexible renforcé de filetage.
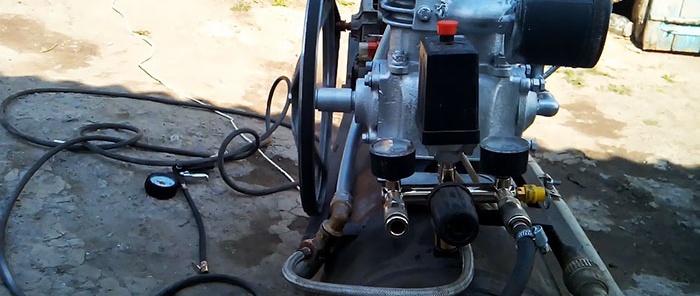
Nous installons un filtre à air constitué d'un pot en plastique avec un couvercle percé de trous sur le tuyau d'aspiration du compresseur.
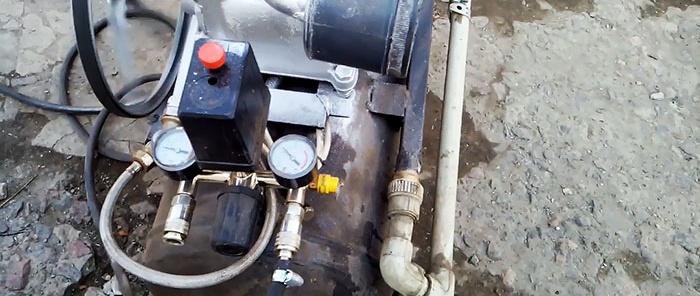
À l’autre extrémité du tuyau, nous montons un pistolet de gonflage des pneus.
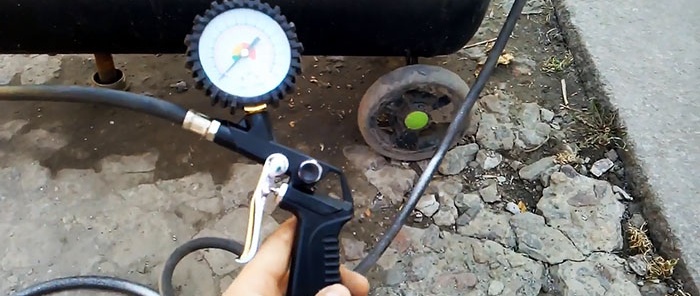
Une éponge en mousse découpée sur mesure est utilisée comme élément filtrant.
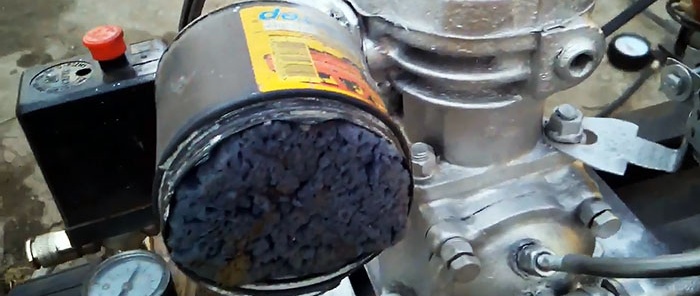
Le rapport des poulies motrice et menée est de 1 à 13, ce qui permet de réduire les 13 000 tr/min du moteur électrique à 1 000 tr/min sur le compresseur.
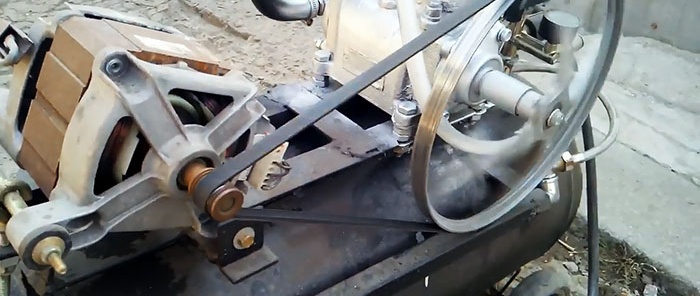
Cela garantit le fonctionnement normal de l'unité et une montée rapide de la pression dans le récepteur. Automatique dès que 6 atm sont atteints. coupe l'alimentation électrique du variateur et, à mesure que la consommation d'air augmente, le cycle se répète.
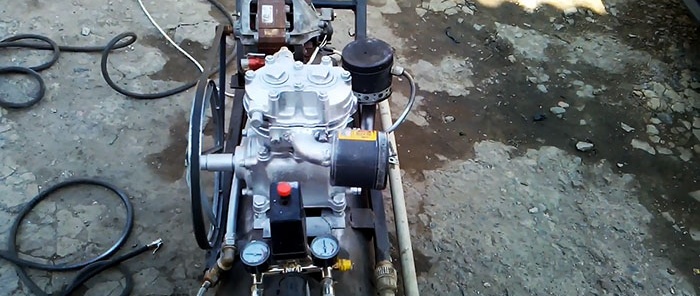
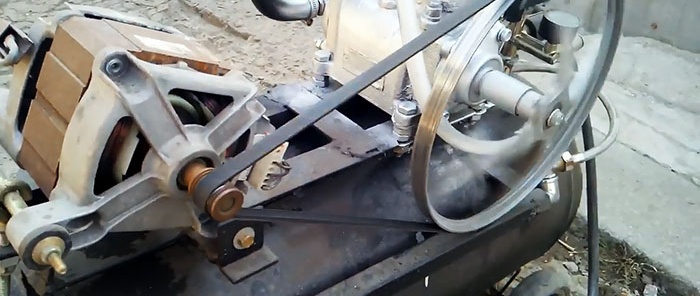
Matériaux, composants et outils utilisés
Le processus de fabrication d’un compresseur d’air nécessite des compétences en métallurgie et en plomberie de la part d’un artisan. Pour les travaux, un certain nombre de composants et de pièces ont été nécessaires : neufs ou d'occasion :
- Compresseur pour camion ZIL-130 ou ZIL-131.
- Moteur électrique d'une puissance nominale de 300 W, monophasé, tension 220 V.
- Grandes et petites poulies.
- Récepteur : cylindre en acier.
- Systèmes de contrôle automatique fabriqués en Chine avec manomètres.
- Raccords de plomberie : tés à pince, coudes et clapet anti-retour.
- Tubes profilés en acier, métal-plastique et plastique.
Pour effectuer le travail, vous aurez besoin d'un outil de mécanicien, d'une perceuse avec un jeu de perceuses et d'une soudure électrique. Certaines opérations, par exemple l'alésage d'une poulie, sont commandées dans un atelier spécialisé.
La procédure de fabrication et d'assemblage du compresseur
La plupart des composants ont été utilisés, nettoyés des contaminants et, si nécessaire, reconstruits. Les principales pièces du compresseur ont été fabriquées dans le garage et assemblées dans l'ordre suivant :
L'unité automobile est montée sur le châssis du récepteur à l'aide de connexions boulonnées.
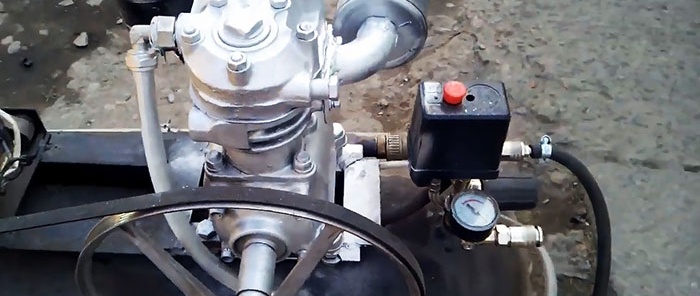
Un entraînement électrique est installé à côté pour que les poulies soient dans le même plan.
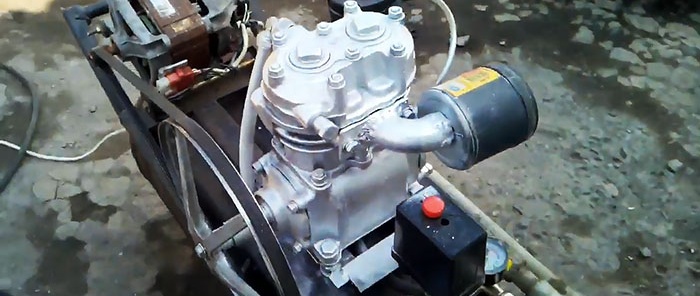
Devant le compresseur sur le châssis, nous montons le système de contrôle automatique et le reconfigurons : mise en marche à une pression de 4 atm, arrêt à 6 atm.
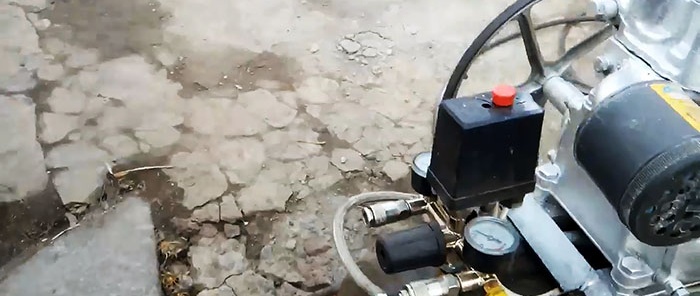
Nous perçons un trou dans le couvercle du carter du compresseur, coupons un filetage et vissons un carré. Nous y attachons un tube avec un réservoir d'huile et, au-dessus, nous découpons un reniflard à travers lequel l'huile sera expulsée dans le réservoir de stockage.
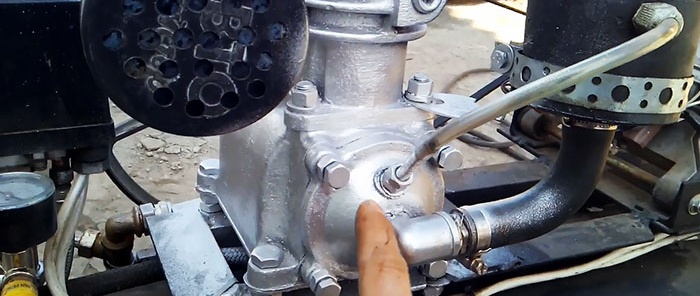
Nous soudons un radiateur de refroidissement à air à partir de tubes en acier, qui sert simultanément de poignée pour le transport. D'un côté, nous y connectons la sortie du compresseur, de l'autre, nous connectons le tube d'alimentation en air au récepteur.
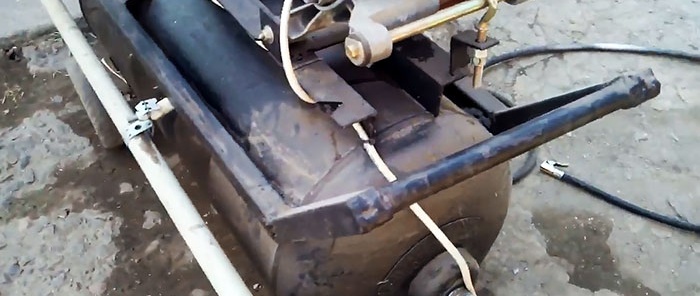
Nous tournons la conduite d'air à l'aide de deux carrés.
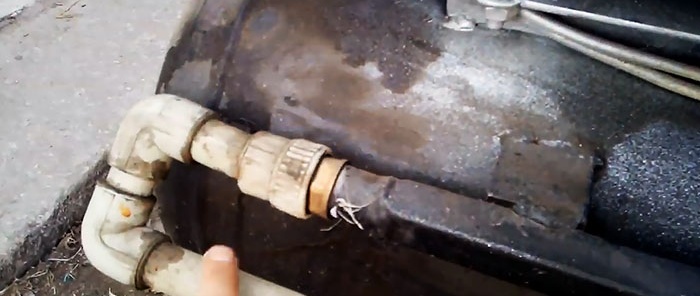
Nous installons un clapet anti-retour à l'entrée du récepteur.
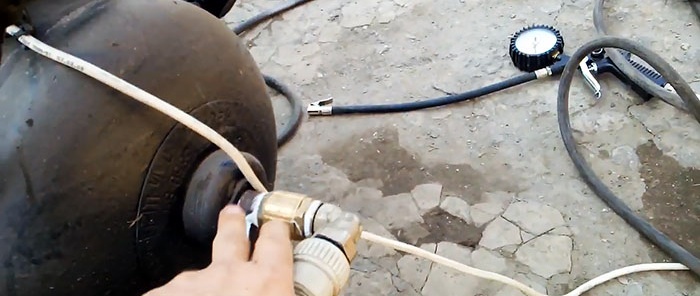
A la sortie du récepteur, installez une vanne et raccordez un tuyau flexible renforcé de filetage.
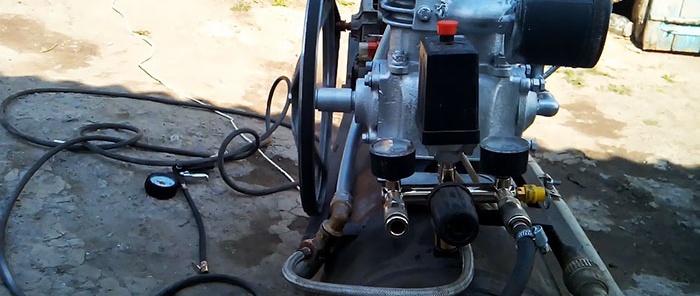
Nous installons un filtre à air constitué d'un pot en plastique avec un couvercle percé de trous sur le tuyau d'aspiration du compresseur.
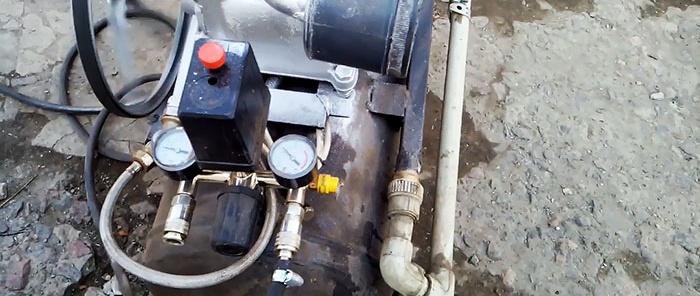
À l’autre extrémité du tuyau, nous montons un pistolet de gonflage des pneus.
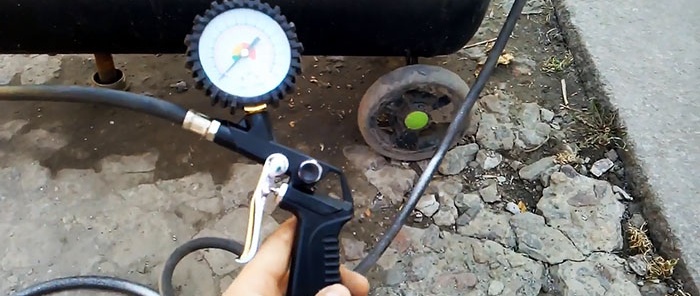
Une éponge en mousse découpée sur mesure est utilisée comme élément filtrant.
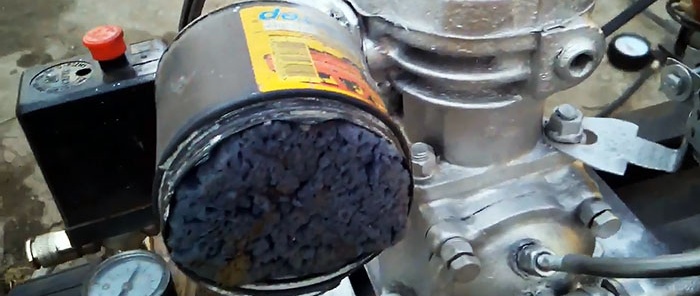
Le rapport des poulies motrice et menée est de 1 à 13, ce qui permet de réduire les 13 000 tr/min du moteur électrique à 1 000 tr/min sur le compresseur.
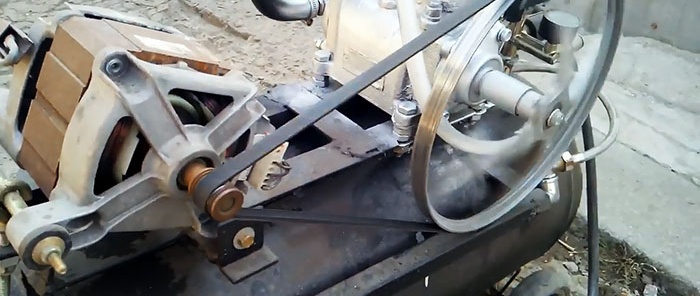
Cela garantit le fonctionnement normal de l'unité et une montée rapide de la pression dans le récepteur. Automatique dès que 6 atm sont atteints. coupe l'alimentation électrique du variateur et, à mesure que la consommation d'air augmente, le cycle se répète.
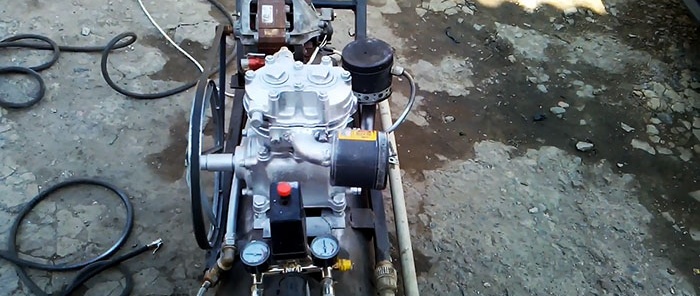
Voir la vidéo
Classes de maître similaires
Particulièrement intéressant
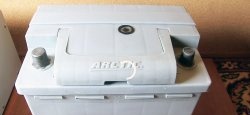
Le moyen le plus efficace de restaurer votre batterie
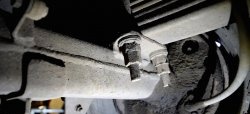
Le lubrifiant pénétrant le plus puissant
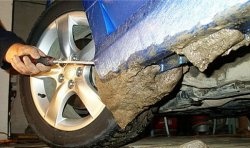
Un moyen simple de se débarrasser de la saleté collée aux doublures d'ailes et
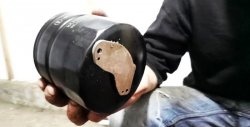
Vaut-il la peine d'installer un aimant sur le filtre à huile ?
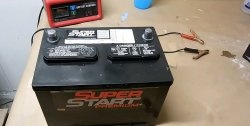
Comment restaurer une batterie de voiture avec du bicarbonate de soude
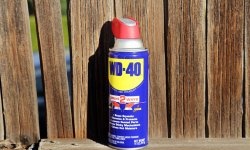
Utilisations inhabituelles du WD-40
Commentaires (1)