Brass soldering technology
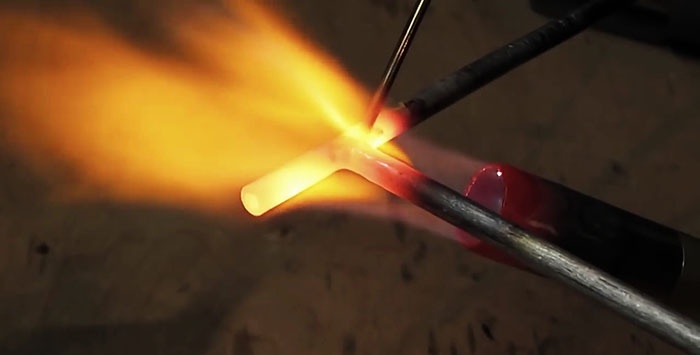
The method of strong soldering of products made of various metals is carried out by heating the soldered parts with a gas burner and using brass as solder. With the widespread use of copper car radiators, soldering with brass was the only reliable way to eliminate leaks. This type of soldering is widely used in the manufacture and repair of household and industrial equipment and air conditioners. In addition, brass soldering allows you to securely fasten refractory cutting parts to the body of a cutter or drill string. Soldering with brass allows you to assemble small hand-forged artistic products (chandeliers, fireplace grates, etc.).
Materials and tools
Soldering with brass is carried out using three main components: a gas burner, giving a temperature of at least 1000 degrees.
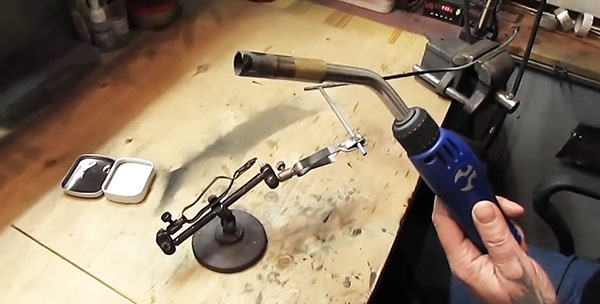
Brass solder (in the form of wire or tape).
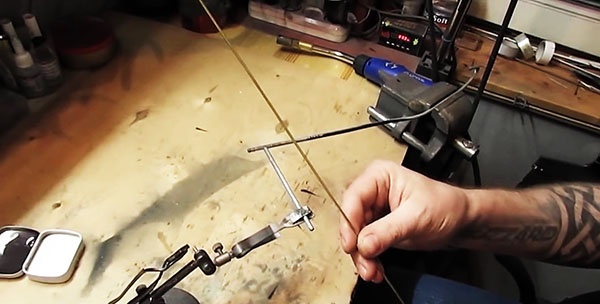
And flux - sodium tetraborate or borax, mixed with boric acid powder.
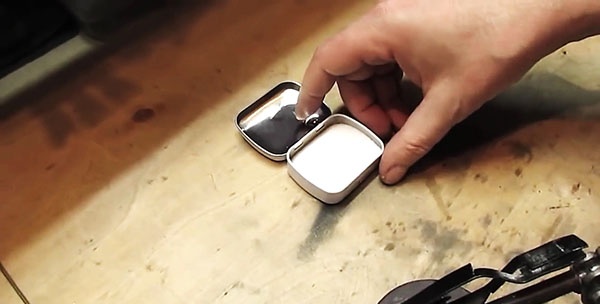
Modern household gas burners use purified propane, sold in mini cylinders, or special mixtures of gases. More complex torches with separate gas and oxygen supplies speed up heating and the entire soldering process.
The need for this flux is determined by the zinc content of brass.Zinc, when melting brass wire without borax, causes the solder to boil, which affects the quality of the seam and its strength properties.
In addition to the main components, we will need auxiliary tools:
- sandpaper and files for cleaning parts;
- various vices and clamps;
- holding hand tools (pliers, long-nose pliers, etc.);
- liquids for degreasing and washing and removing scale from finished seams (acid solutions);
- fireproof gloves and other personal protective equipment used during welding work.
When carrying out open hot work, fire safety rules must be strictly observed. You must have a fire extinguisher, water, and asbestos cloth or tarpaulin in the room. It should be remembered that zinc vapor is poisonous. Personal protective equipment, breaks in work and ventilation of the room are necessary.
Brass soldering process
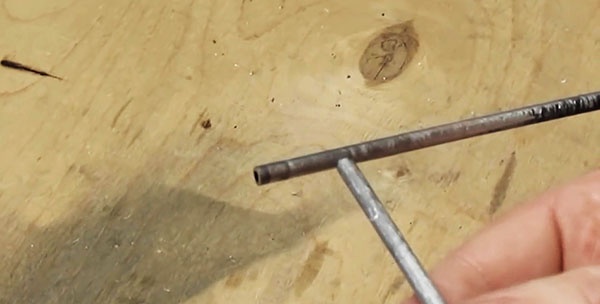
It is necessary to prepare the parts to be soldered. Let's say we need to make a small frame structure from thin-walled steel tubes with a diameter of approximately 5 mm. When soldering two small-diameter tubes end-to-end, you need to make a notch in the end of the soldered tube. This will increase the strength of the connection. The parts must be placed in clamping devices and the connections pressed together. This is a necessary condition for performing high-quality soldering with brass solder, since your hands will be busy with the torch and the supply of solder.
We light the gas burner and begin to heat the soldering area until a red color appears.
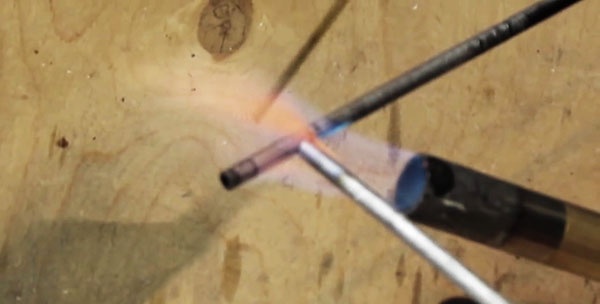
We also heat the brass wire (solder) and lower the heated end of the solder into the borax. Borax sticks to the solder wire.
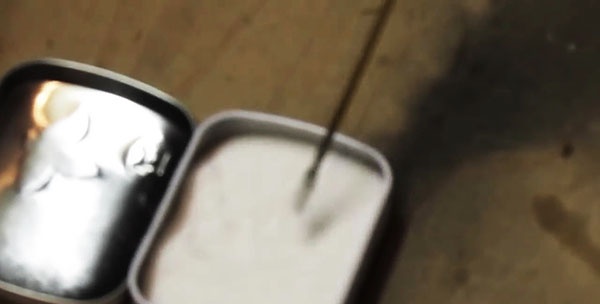
We briefly move the burner flame back and apply flux directly to the junction of the steel tubes. Borax melts quickly and covers the entire soldering area. If you do not remove the flame, the borax will simply blow away from the brass wire.
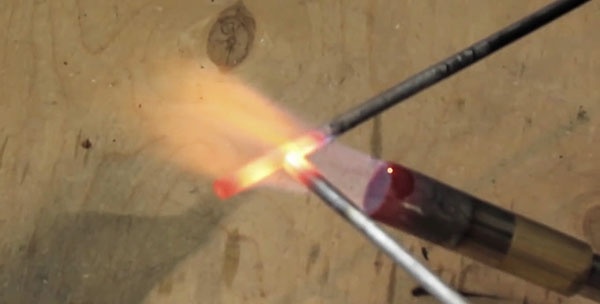
After this, soldering begins - slowly melting the brass solder, manually feeding it and filling the joint between the parts.
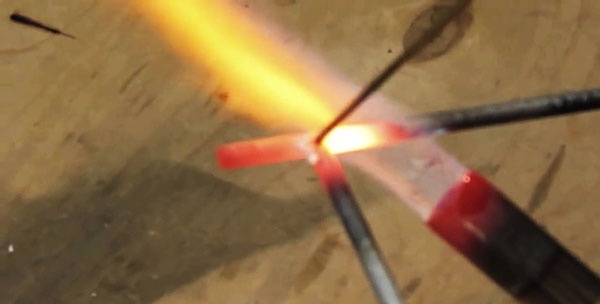
During work, visual control of the quality of the seam is carried out. If a fistula or an area not covered by solder is found in the lower part. It is better to turn the part over and solder this place again.
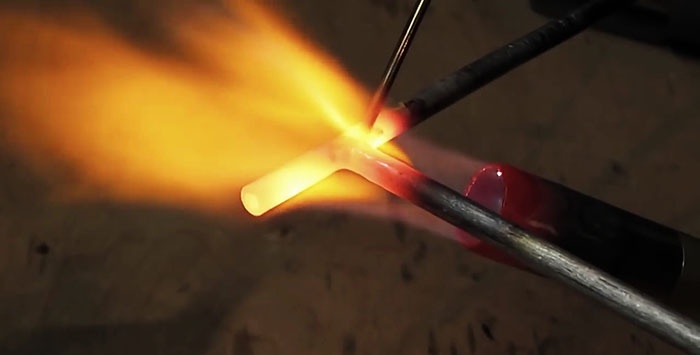
After filling the hands, you can solder the “ceiling” joints. The soldered parts must be allowed to cool in air.

Then you need to remove scale by placing the part in a solution of food grade citric acid.
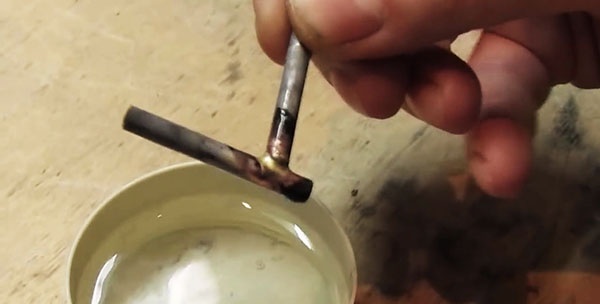
To check the quality of the seam, we bend the product.
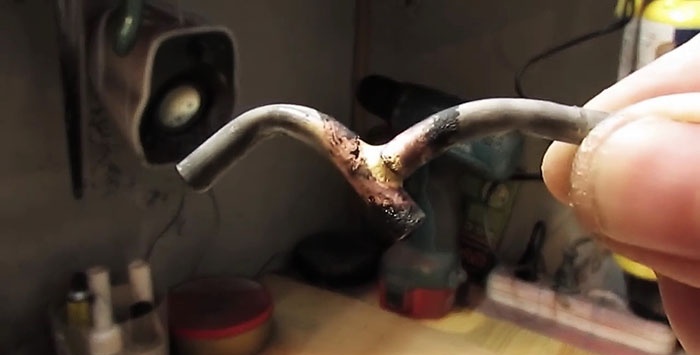
Very durable!
Precautionary measures
Soldering with brass is an open hot work. Strict compliance with all fire protection measures is necessary. In addition, working with zinc vapor can cause severe poisoning of the body. Protective measures must be taken. Mini gas cylinders may have leaks in the valve, which leads to explosions and fires. Constant monitoring of the operation of the gas burner is necessary.
Watch the video
Similar master classes
Particularly interesting
Comments (4)