How to make a router from a grinder
Like any professional equipment, a router costs a lot of money. It is mainly used in the manufacture furniture. For use at home, it can be made on the basis of an angle grinder (angle grinder).
Along with the grinder, we will prepare the following materials and parts:
To work on a homemade product, you cannot do without the following tools and devices: calipers, square and tape measure; lathe and drilling machines; welding; saw on metal and wood; taps with a collar; sandpaper; height adjuster, etc.
Let's start working with the drive - a retrofitted angle grinder. Other important components of the router are the vertical guide rods and the sole. A regular drill chuck cannot be mounted on an angle grinder spindle, since their threads do not match and are equal to M12 and M14, respectively. Using the attachment, we fix the drill chuck on the lathe and drill a hole for the M14 thread.
Thread cutting can be done not only on a machine, but also manually.
We easily screw the chuck onto the spindle thread, but we see that it rests against the centering belt. We drill the entrance into the threaded hole of the cartridge to the diameter and height of the centering belt.
This allows you to securely secure the cartridge to the threads of the angle grinder spindle without wobbling, even by hand. Our drive for the future router is ready.
We mark a rod of suitable diameter and length for the vertical rod blanks. We turn it on a lathe to the required size and process it with sandpaper.
Using a metal saw, we cut blanks for vertical guide rods.
From a thicker rod we prepare two pieces of the required length and drill longitudinal holes in them to suit the size of the rods.
We check the vertical position of the rods with a square, put springs and guides on them, and imitate their operation.
We mark the sheet of plexiglass and cut out two identical plates using a wood circular saw.
We remove the protective film from them, wipe them with a rag, apply a drop of glue to one of the plates in the corners, and press the other one on top. In the double plate, we drill four holes in the corners, form sockets for the screw heads, which we screw in flush to secure the connection of the plates.
According to the markings in the plexiglass plates, we drill holes for the rods in two passes.
We end the rods on a lathe, drill holes for the threads, which we cut manually with a tap.
We install rods into the plate sockets and secure them with a metal plate on top.
From a thick strip of metal we cut two identical elements with drilled holes and bend them in a special vice at a certain angle.
We bolt the bent plates on both sides to the body of the angle grinder, using the standard holes for the handle. We install the grinder with a chuck and a clamped cutter in the center of the sole. We place the height adjuster under the other end of the angle grinder and set the angle grinder to a horizontal position. We weld the bent ends of the plates to the tubes sliding along the rods in pre-designated places.
In the center of the plate-sole, we drill a hole with an annular drill, designed for the largest diameter of the cutter used.
We bend a bracket from a thick strip of metal and weld it horizontally to the sliding tubes in front.
Having removed the rods from the sliding tubes, we drill holes on the side, cut the threads and screw in the wing-head bolts.
We remove the sole and drill from the end to the holes for the rods at right angles, cut the threads and screw in the bolts.
We return the sole back and tighten the bolts, securing the rods in the holes. We weld an eyelet to the transverse bracket in the center, onto which we attach a stop handle, consisting of two halves.
We replace the temporary bar that tightens the rods with a bracket, but before strengthening it, we lift it up along the rods and remove the drive with sliding tubes and springs in order to install thrust bushings. We reassemble the removed components and parts in the reverse order, finally tighten the bracket and screw the handle.
Having installed the cutter in the working position, we fix it by tightening the bolts with wing heads screwed into the sliding tubes, and check the operation of the cutter in action.
Will need
Along with the grinder, we will prepare the following materials and parts:
- drill chuck;
- metal rods;
- thrust springs and bushings;
- plexiglass;
- metal strip;
- plastic handle;
- screws, bolts, wing nuts;
- glue and rags.
To work on a homemade product, you cannot do without the following tools and devices: calipers, square and tape measure; lathe and drilling machines; welding; saw on metal and wood; taps with a collar; sandpaper; height adjuster, etc.
The procedure for manufacturing components and assembling the router
Let's start working with the drive - a retrofitted angle grinder. Other important components of the router are the vertical guide rods and the sole. A regular drill chuck cannot be mounted on an angle grinder spindle, since their threads do not match and are equal to M12 and M14, respectively. Using the attachment, we fix the drill chuck on the lathe and drill a hole for the M14 thread.
Thread cutting can be done not only on a machine, but also manually.
We easily screw the chuck onto the spindle thread, but we see that it rests against the centering belt. We drill the entrance into the threaded hole of the cartridge to the diameter and height of the centering belt.
This allows you to securely secure the cartridge to the threads of the angle grinder spindle without wobbling, even by hand. Our drive for the future router is ready.
We mark a rod of suitable diameter and length for the vertical rod blanks. We turn it on a lathe to the required size and process it with sandpaper.
Using a metal saw, we cut blanks for vertical guide rods.
From a thicker rod we prepare two pieces of the required length and drill longitudinal holes in them to suit the size of the rods.
We check the vertical position of the rods with a square, put springs and guides on them, and imitate their operation.
We mark the sheet of plexiglass and cut out two identical plates using a wood circular saw.
We remove the protective film from them, wipe them with a rag, apply a drop of glue to one of the plates in the corners, and press the other one on top. In the double plate, we drill four holes in the corners, form sockets for the screw heads, which we screw in flush to secure the connection of the plates.
According to the markings in the plexiglass plates, we drill holes for the rods in two passes.
We end the rods on a lathe, drill holes for the threads, which we cut manually with a tap.
We install rods into the plate sockets and secure them with a metal plate on top.
From a thick strip of metal we cut two identical elements with drilled holes and bend them in a special vice at a certain angle.
We bolt the bent plates on both sides to the body of the angle grinder, using the standard holes for the handle. We install the grinder with a chuck and a clamped cutter in the center of the sole. We place the height adjuster under the other end of the angle grinder and set the angle grinder to a horizontal position. We weld the bent ends of the plates to the tubes sliding along the rods in pre-designated places.
In the center of the plate-sole, we drill a hole with an annular drill, designed for the largest diameter of the cutter used.
We bend a bracket from a thick strip of metal and weld it horizontally to the sliding tubes in front.
Having removed the rods from the sliding tubes, we drill holes on the side, cut the threads and screw in the wing-head bolts.
We remove the sole and drill from the end to the holes for the rods at right angles, cut the threads and screw in the bolts.
We return the sole back and tighten the bolts, securing the rods in the holes. We weld an eyelet to the transverse bracket in the center, onto which we attach a stop handle, consisting of two halves.
We replace the temporary bar that tightens the rods with a bracket, but before strengthening it, we lift it up along the rods and remove the drive with sliding tubes and springs in order to install thrust bushings. We reassemble the removed components and parts in the reverse order, finally tighten the bracket and screw the handle.
Having installed the cutter in the working position, we fix it by tightening the bolts with wing heads screwed into the sliding tubes, and check the operation of the cutter in action.
Watch the video
Similar master classes
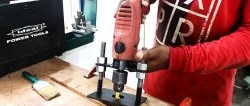
How to turn a drill into a router using simple equipment
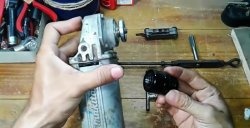
How to install a drill chuck on an angle grinder and why it can
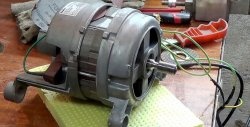
Powerful cutter from a washing machine engine
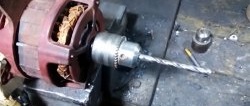
How to remove a pressed pulley from an electric motor and install
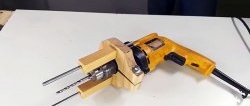
Auto centering machine for drill
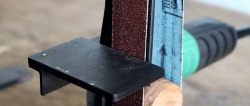
How to make a belt grinder without welding on the base
Particularly interesting
Comments (2)