An easy way to make any springs
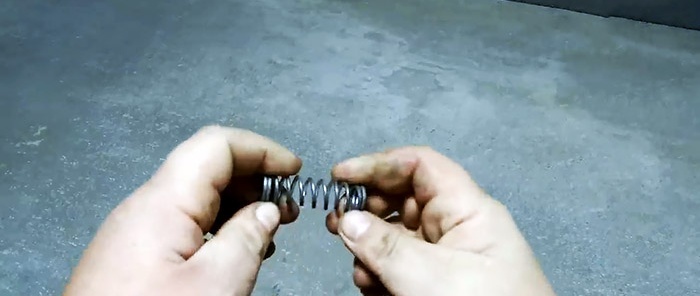
Many mechanisms use a non-standard spring, which, if worn, cannot be replaced due to its unavailability. In this case, you can do it yourself, without wasting time looking for similar analogues that require trimming.
Tools and materials:
- doorstop;
- gas-burner;
- pliers;
- screwdriver;
- machine oil;
- a rod or bolt corresponding to the diameter of the required spring.
Manufacturing a custom spring
For work you will need wire made of specialized steel 65G or similar. As its source, you can use a piece from a regular door spring, since it is sold in any hardware and construction store.
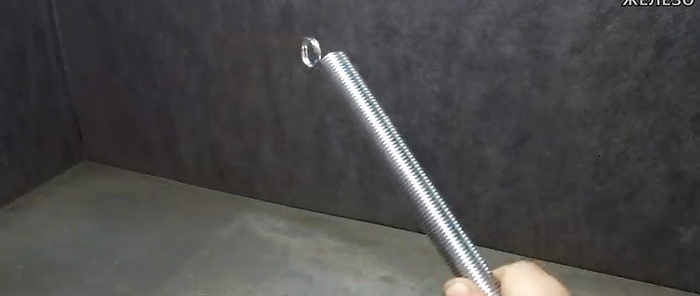
To unwind it, you need to anneal the steel, making it flexible. To do this, it is heated to a dark red color with a gas burner, blowtorch or in a forge, after which it is left to cool in the air.

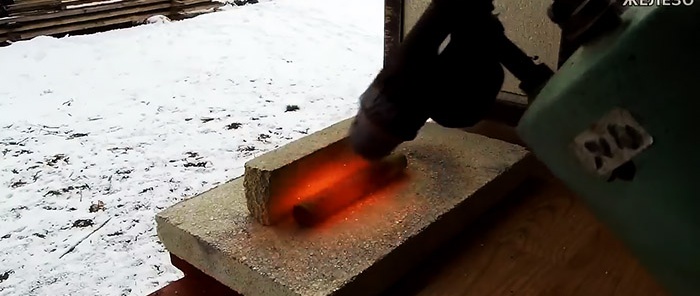
The slowly cooled steel is released, so the spring easily unwinds into wire.
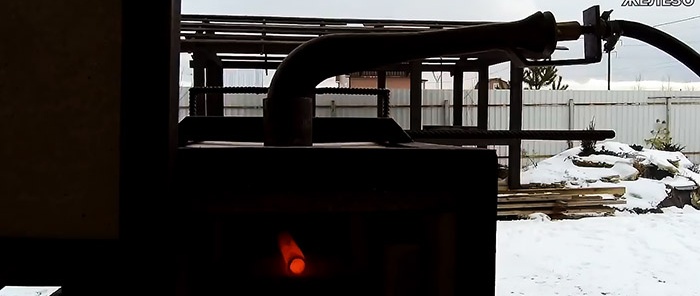
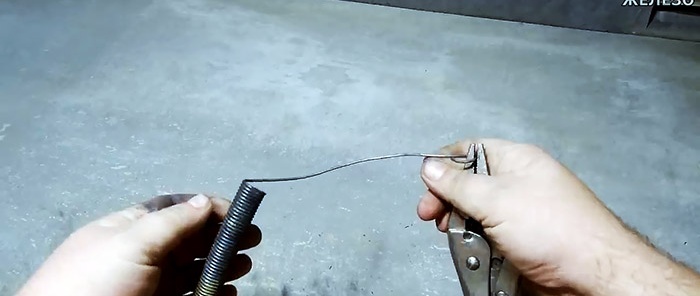
After this, a mandrel is taken that corresponds to the inner diameter of the non-standard spring that needs to be made, and the wire is wound onto it close turn to turn.Winding is done under tension so that the workpiece receives the correct cylindrical shape.
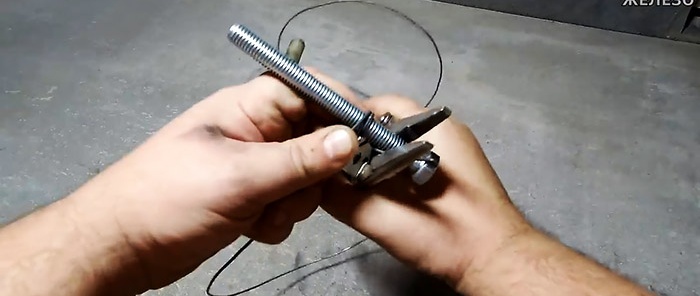
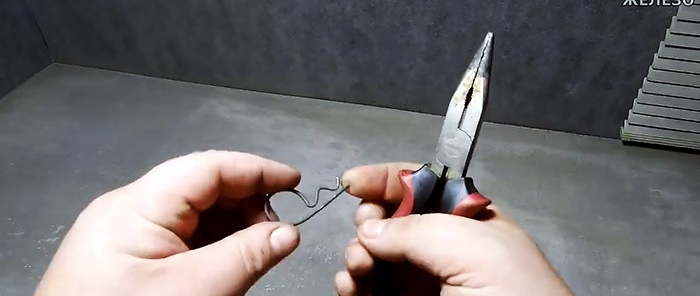
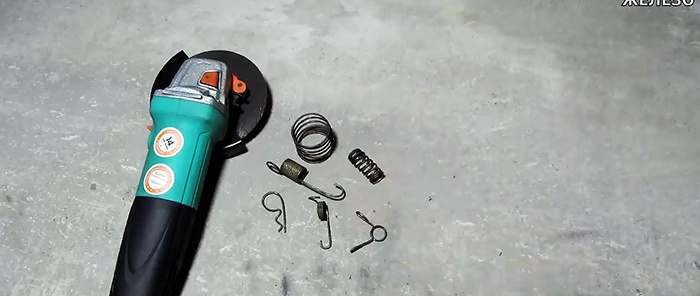
After winding, the spring is removed from the mandrel. If it must work in tension, then eyes are made at its ends. When a compression spring is needed, the coils should be separated. To do this, insert a screwdriver between them and use it to create the required distance. The first and last turns of the pressure spring should be tight, and the center should have a routing. In this case, it will work in the right direction, without trying to jump to the side. When the workpiece acquires the required shape, it can be cut.
Next, the steel needs to regain its elasticity. To do this, it is heated to a dark red color and quickly dropped into the oil. After hardening, the metal becomes hard.
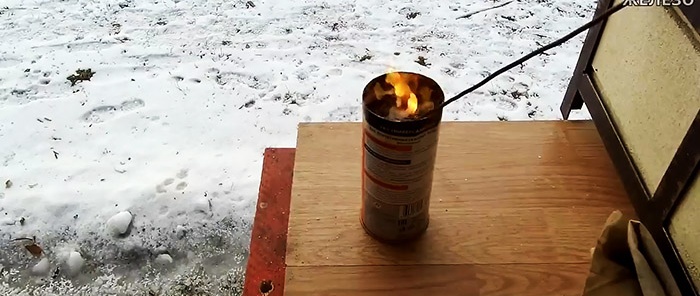
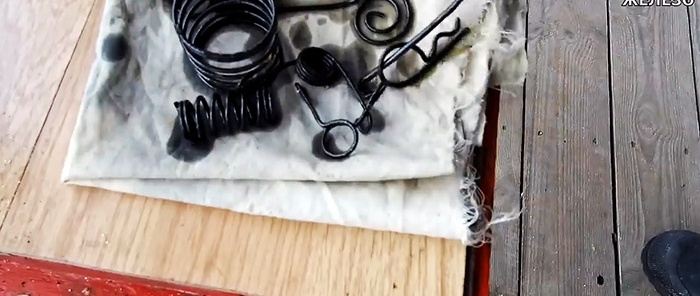
A hardened spring is brittle. In order for it to obtain an optimal balance between hardness and elasticity, a high tempering is required. To do this, the workpiece is heated to a temperature of 400-500 degrees Celsius. You can determine that it is hot enough by its color. First, the spring will turn light cornflower blue, and then light gray, which signals that the desired temperature has been reached. After heating, it is cooled in air.
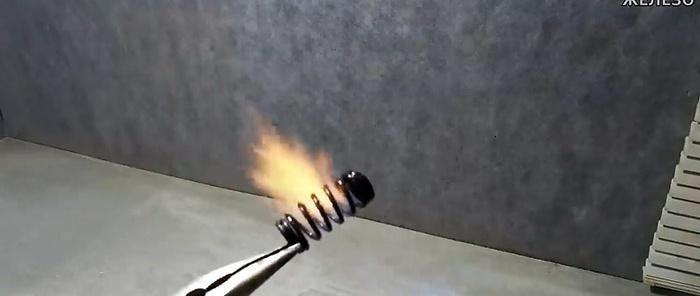
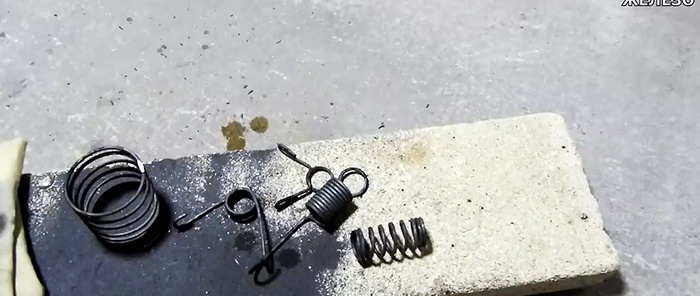
A spring made in this way is stiff and elastic. Compliance with the proposed guidelines during annealing, hardening and tempering will make it possible to practically recreate the factory production technology. Thanks to this, a homemade spring is in no way inferior to purchased products.
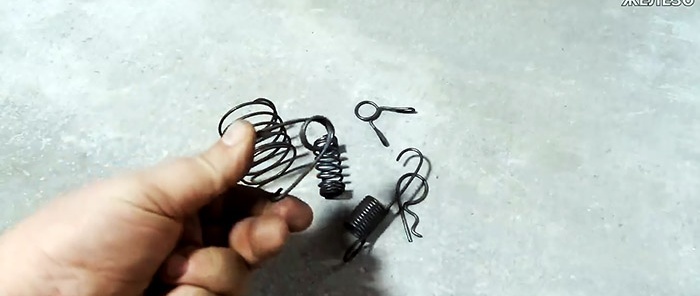
Watch the video
Similar master classes
Particularly interesting
Comments (0)