Paving slabs without vibrating table and molds in food trays
If you want to lay paving slabs on a small area, you can cast them yourself. It will be cheaper than buying it and not very time-consuming. For this, a simple technology is used that practically does not require any equipment.
Materials:
- Cement;
- sand;
- plasticizer for concrete;
- colored powder pigment for concrete;
- working off;
- disposable food containers.
Paving slab production process
To cast the tiles, you will need to prepare concrete based on cement and ravine sand with pebbles in a ratio of 1:2.5.
If you use clean fine sand, you can also add 3 parts of crushed stone. Water and plasticizer are poured into the mixture.
The latter is added according to the instructions. The concrete should be thick but fluid. Since this is a cottage industry without many molds, there is no need to prepare a lot of concrete. Half a bucket is enough to start with.
Powdered pigment is added to the concrete.
The composition is mixed again until a uniform color is obtained.Then you need to lubricate the disposable food trays using a brush. During production, you can make tiles of different colors, so that later when laying you can form the desired pattern.
Concrete is poured into greased molds.
You can not fill it completely if the trays are high. A layer of 5 cm is sufficient.
Then you need to compact the concrete. In production, this is done on a vibrating table, but if you only need a couple of square meters of tiles, then it is not practical to make it. In this case, try placing the tiles on the table, and place a sander running at low speed under the tabletop. This will compact the concrete quite well.
An easier option would be to install a sheet of metal onto a working country washing machine, on which the trays are placed. In this case, you can wash clothes and compact concrete at the same time.
If there is no mechanized way to compact the concrete, then you can shake the trays manually one by one. This is done until no more air bubbles come out of the concrete.
Forms with compacted concrete must be placed on a level base, for example, a pallet. Drying should take place in the shade. The molds are covered with film to reduce water evaporation. On top, if animals are walking nearby, any sheet material should be laid so that they do not walk on the soft concrete.
On the second day, or better yet after two days, the finished tiles are removed from the molds. This is done carefully so as not to jam the plastic. Then a new batch is poured.
Thus, depending on the number of forms, you can make one or a couple of square meters of tiles every day.Since it is cast from containers, it has a very unusual corrugated front side, which compares favorably with store-bought analogues.
Watch the video
Similar master classes
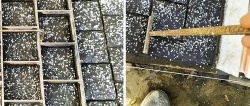
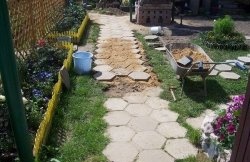

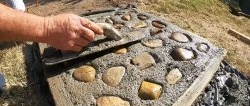
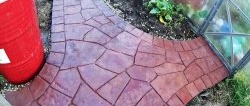
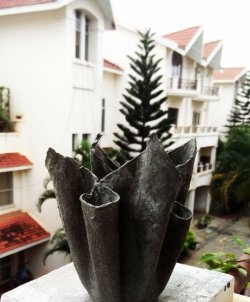
Particularly interesting
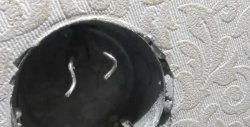
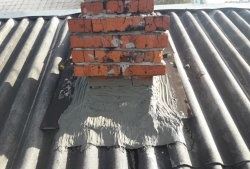
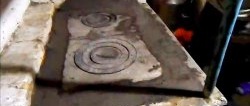
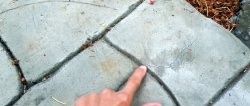
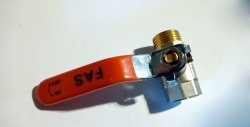
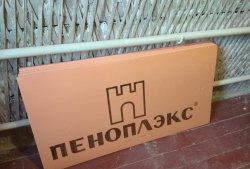