4 Surprisingly Useful Inventions for the Workshop
Often, home-made devices of original design turn out to be more convenient than factory-made analogues, or at a lower manufacturing cost they are completely as good as them. That is why many often make the necessary devices with their own hands, refusing purchased ones. This collection includes 4 useful ideas that are worth repeating in your workshop.
1. Soldering nozzle for PP pipes on a hair dryer
The heat gun heats up strongly enough to melt PP pipes. Therefore, having made a simple attachment, they can be soldered using it. To do this, take a piece of profile pipe and weld its edges with sheet metal inserts.
Long-lasting discs for angle grinders on AliExpress at a discount - http://alii.pub/61bjly
Then we drill one wall of the workpiece in the center and weld a piece of round pipe into it.
We make two holes on the reverse side and cut M6-M8 threads into them.
Now you can screw nozzles for soldering PP pipes to the device. After that, it is attached to the hair dryer using adapters. We start it up and heat up the nozzles, after which we perform soldering.
It is most convenient to secure the device in a vice when working.
2. Manufacturing of laminate, plywood or wooden rings
If you attach several of them to the bit holder, then after drilling you will get rings of different diameters. They turn out to be rough, but can be easily made smooth with sandpaper.
High-quality and durable drills on AliExpress at a discount - http://alii.pub/5zwmxz
3. Pipe sanding drum
The grinding drum can be made from a piece of PP pipe with a diameter of 20 mm. It must be cut lengthwise and the burrs removed. Then sandpaper is rolled onto the workpiece with the grain facing outward, and its edges are inserted into the cut.
Now you can put the drum on the stud and tighten it from the sides with nuts through washers. This will secure the sandpaper and prevent it from falling out. The resulting device is used in conjunction with a drill or drilling machine.
4. Drill chuck welding holder
To make the holder, we select a piece of pipe of such diameter that the drill chuck can fit into it. We drill the workpiece from the side, and weld a thin pipe on top of the hole, which will serve as a handle.
We weld a nut onto the edge of the pipe. After that, screw a long pin into it. It will need to fit into the hole at the end to secure the drill chuck in the chuck.
A nut is welded to the edge of the stud. We weld a washer onto it. The resulting eyelet is used to screw the cable lug from the inverter.
Now all that remains is to insulate the handle and clamp the drill chuck with a pin. After this, the cable is connected to the holder. Clamping the electrodes into the socket is very convenient and quick, and the contact is reliable.
Welding electrodes for general purposes on AliExpress at a discount - http://alii.pub/606j2h
Watch the video
Similar master classes
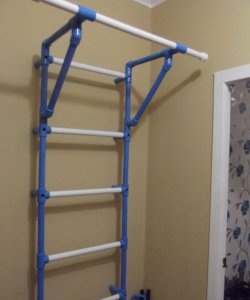
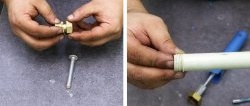
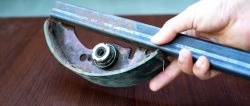
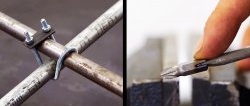

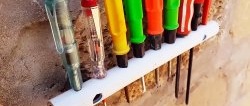