Drill stand for drill from old shock absorbers
A drilling machine is a useful thing, but expensive and bulky, so for most workshops a drill stand is better suited. You can make such a device yourself from old shock absorbers and unnecessary scrap metal.
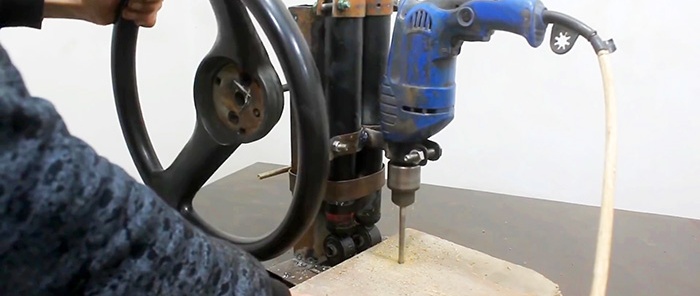
A longitudinal line is drawn on a section of the strip in the center.
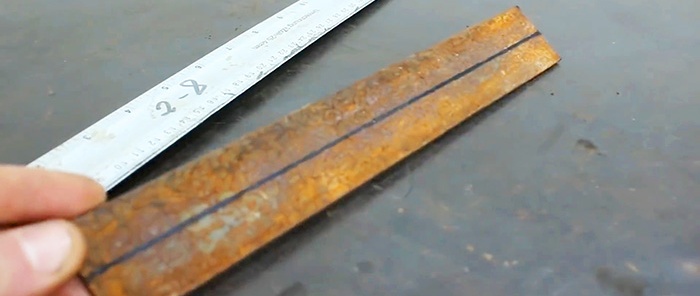
Then a sprocket with teeth soaked in oil is rolled over it.
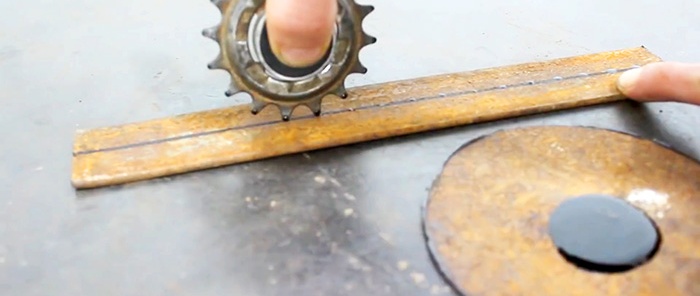
Holes are drilled and countersunk along the remaining mark of the teeth. As a result, the teeth get caught in them during rolling.
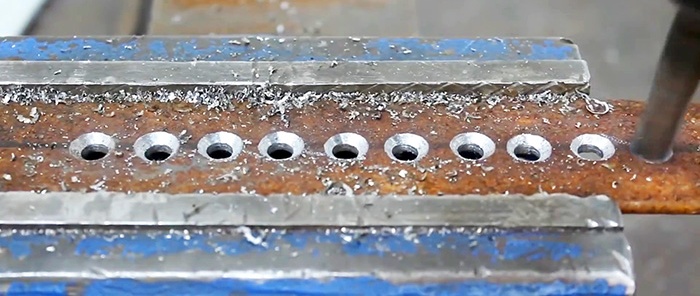
You need to cut 4 strips from sheet steel and bend them into clamps to fit the diameter of the shock absorbers. They are welded to the previously drilled workpiece, joining closely in twos.
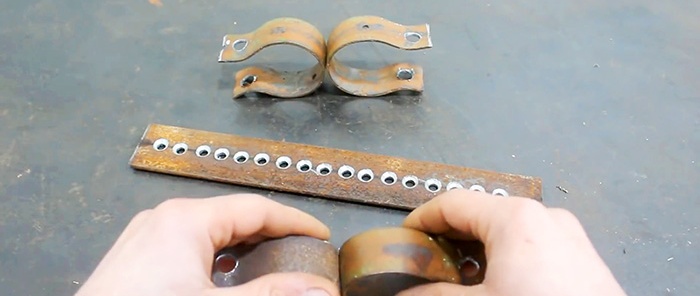
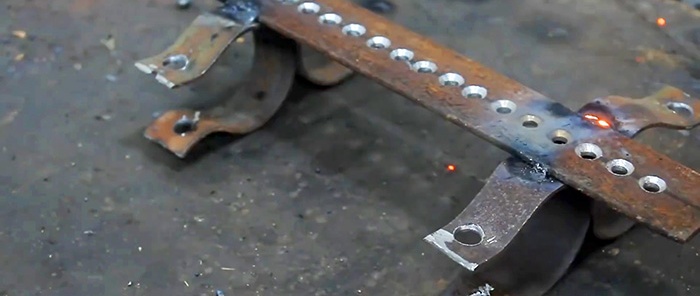
Next, you need to weld the lower eyes of the 2 shock absorbers to the steel plate.
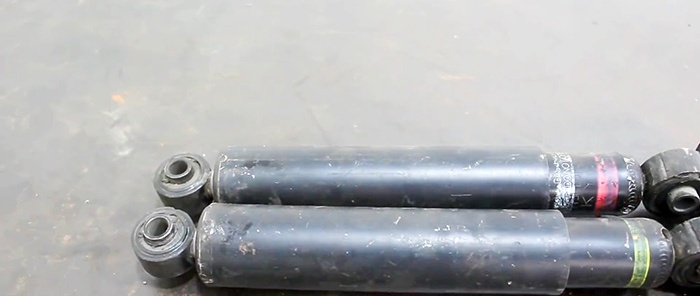
It is important that the shock absorbers move easily, so before doing this they will need to be drilled closer to the bottom to depressurize them. This must be done carefully, since they contain hydraulic fluid under pressure, which will flow in a stream.
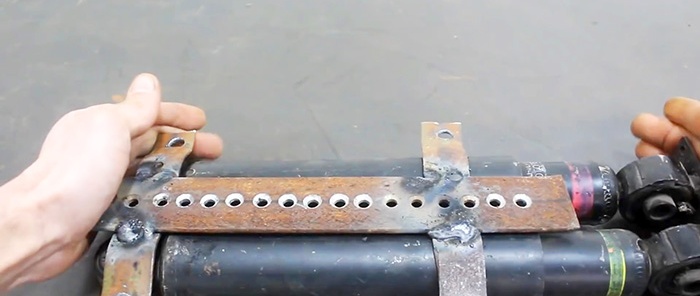
Shock absorbers are installed in clamps welded onto a perforated strip. The clamps are clamped with bolts and nuts on shock absorber tubes of larger diameter. After this, the plate is welded to the base, previously welded from angles or a profile pipe.
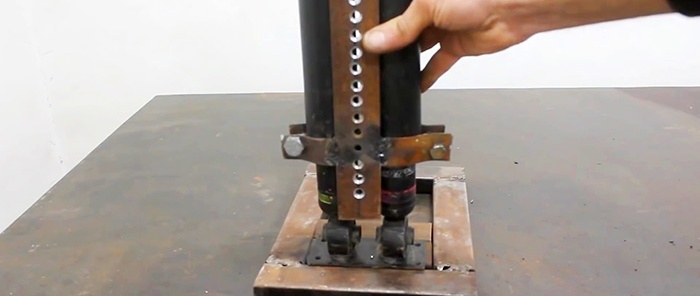
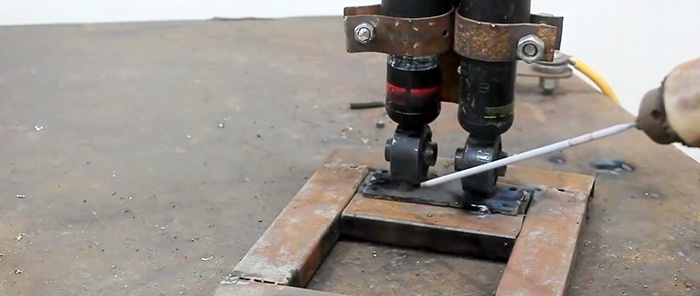
To attach the sprocket to the rack, you need to take a piece of profile pipe, drill a through hole in it and insert a long M10-M14 bolt. An asterisk is put on the bolt and tightened on both sides with nuts.
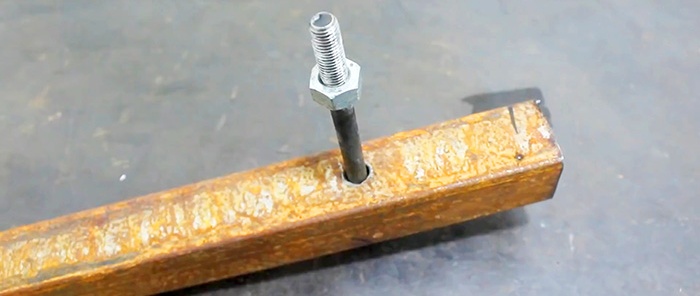
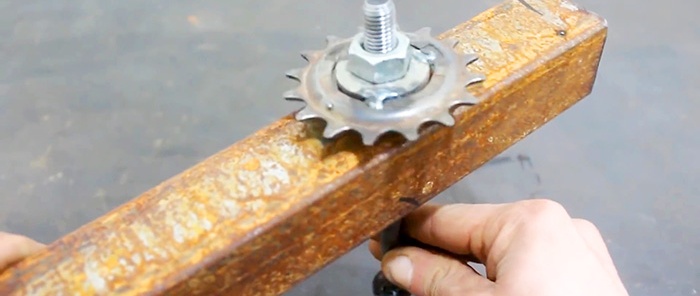
After this, the same piece of profile pipe is cut off and a hole is made in one of its walls opposite the star bolt. The stand is joined and welded onto the base of the stand so that the sprocket fits with its teeth into the perforated holes on the strip.
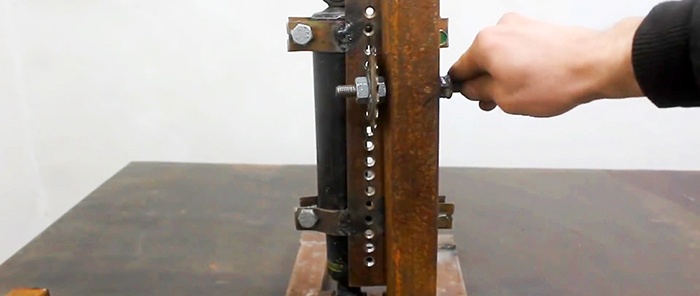
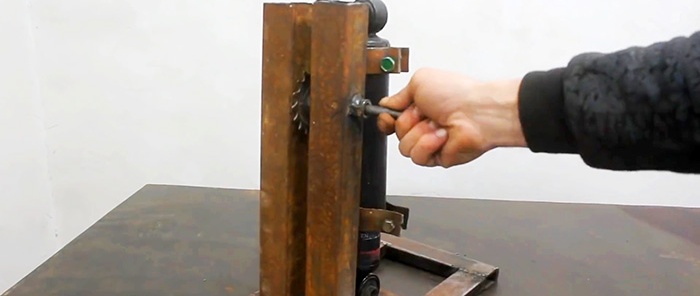
After this, the steering wheel is welded onto the head of the star bolt. To the lower clamps on the shock absorbers you need to weld a clamp on the tube, made to mount the drill body.
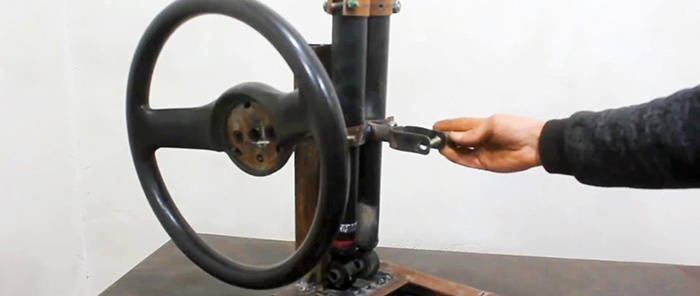
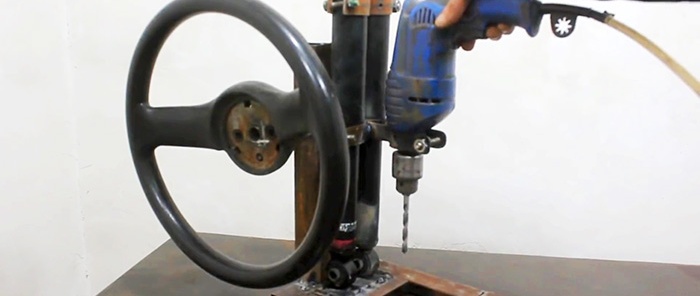
Also, for reliability, you should prepare a large clamp to tighten the shock absorbers with the sprocket stand together.
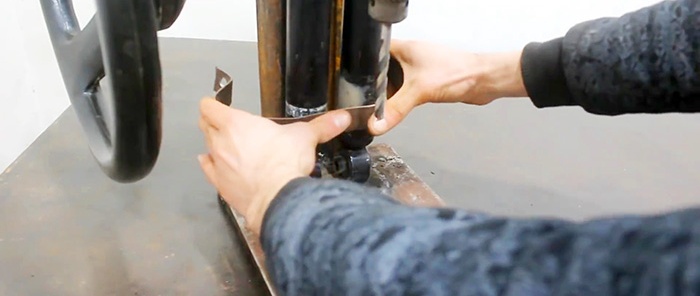
By holding the drill in the stand, you can raise and lower it by rotating the steering wheel. Shock absorbers act as a guide without play, so if the chuck does not dangle, the drilling quality will be close to that of a full-fledged drilling machine.
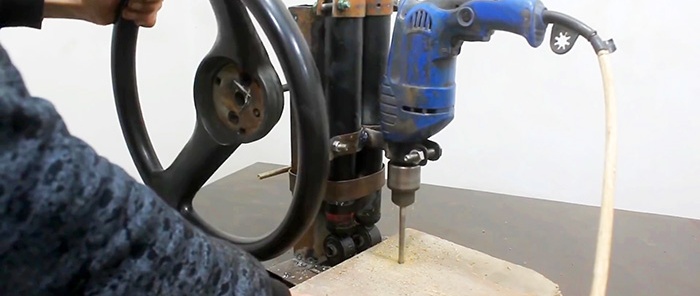
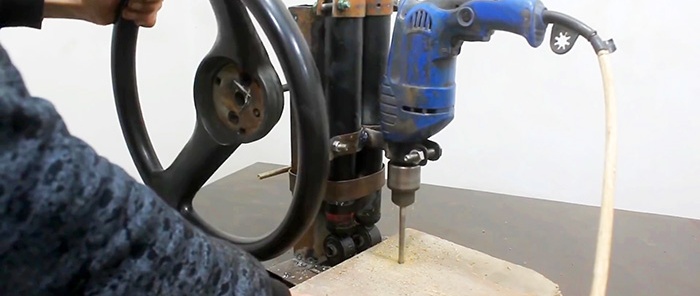
Materials:
- steel strip 30x3 mm or wider;
- sprocket for roller chain;
- sheet steel 2 mm;
- worn shock absorbers – 2 pcs.;
- M8 bolts with nuts – 6 pcs.;
- profile pipe 40x40 mm;
- long bolt with nut M10-M14;
- steering wheel.
Rack manufacturing process
A longitudinal line is drawn on a section of the strip in the center.
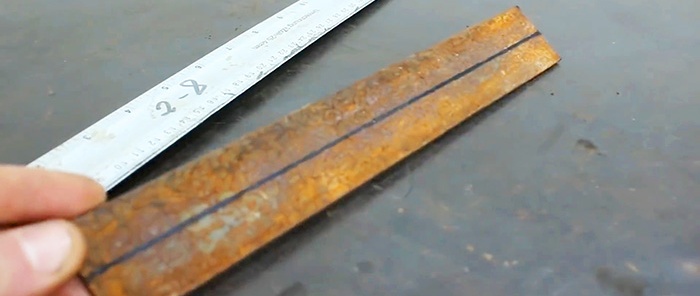
Then a sprocket with teeth soaked in oil is rolled over it.
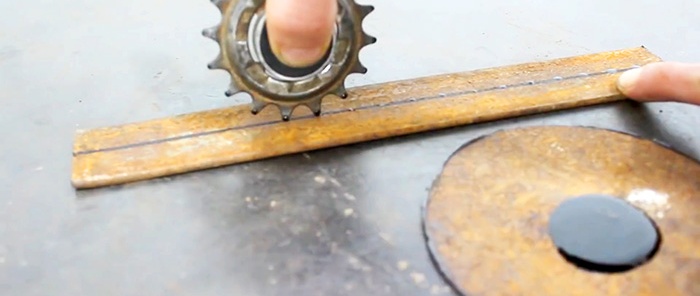
Holes are drilled and countersunk along the remaining mark of the teeth. As a result, the teeth get caught in them during rolling.
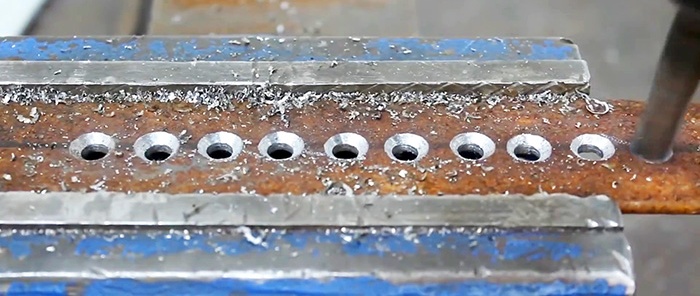
You need to cut 4 strips from sheet steel and bend them into clamps to fit the diameter of the shock absorbers. They are welded to the previously drilled workpiece, joining closely in twos.
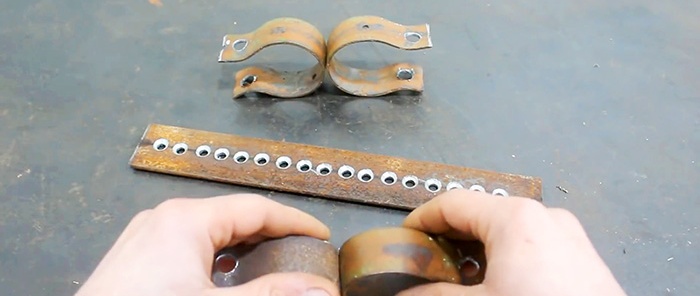
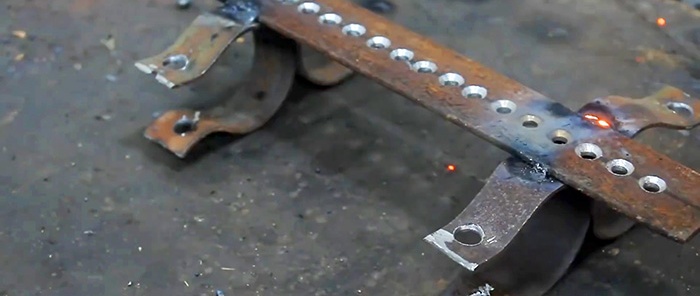
Next, you need to weld the lower eyes of the 2 shock absorbers to the steel plate.
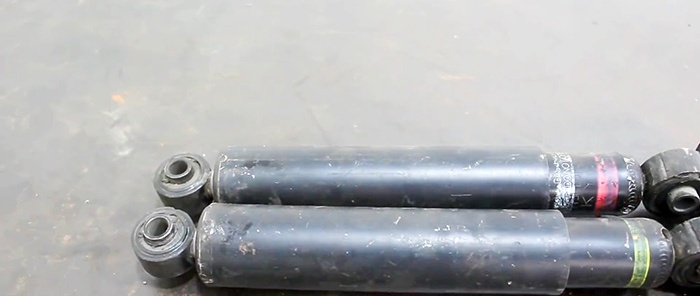
It is important that the shock absorbers move easily, so before doing this they will need to be drilled closer to the bottom to depressurize them. This must be done carefully, since they contain hydraulic fluid under pressure, which will flow in a stream.
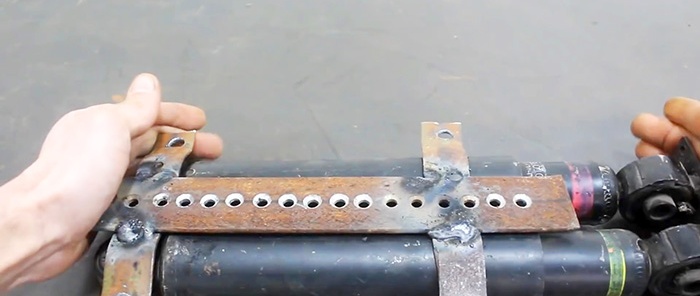
Shock absorbers are installed in clamps welded onto a perforated strip. The clamps are clamped with bolts and nuts on shock absorber tubes of larger diameter. After this, the plate is welded to the base, previously welded from angles or a profile pipe.
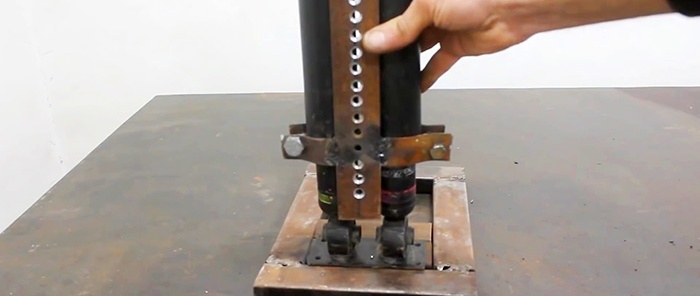
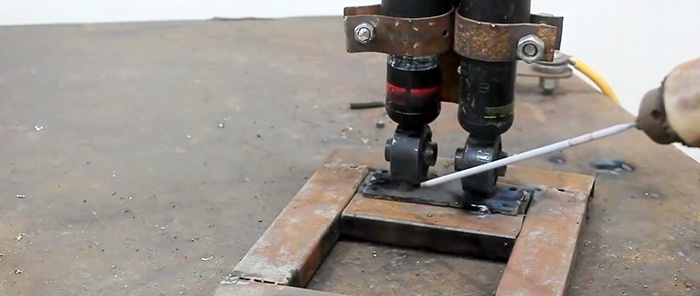
To attach the sprocket to the rack, you need to take a piece of profile pipe, drill a through hole in it and insert a long M10-M14 bolt. An asterisk is put on the bolt and tightened on both sides with nuts.
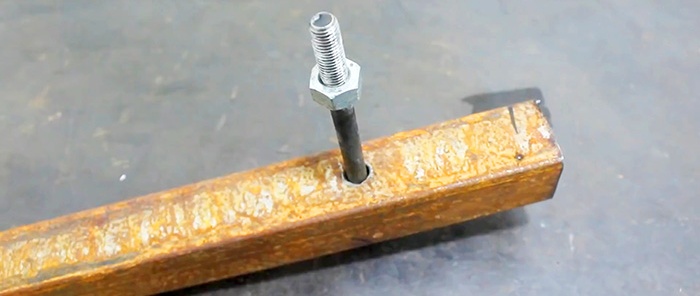
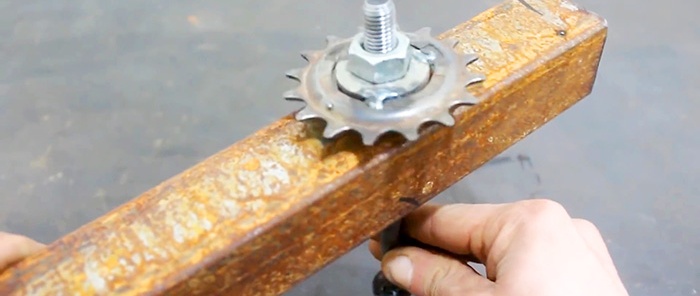
After this, the same piece of profile pipe is cut off and a hole is made in one of its walls opposite the star bolt. The stand is joined and welded onto the base of the stand so that the sprocket fits with its teeth into the perforated holes on the strip.
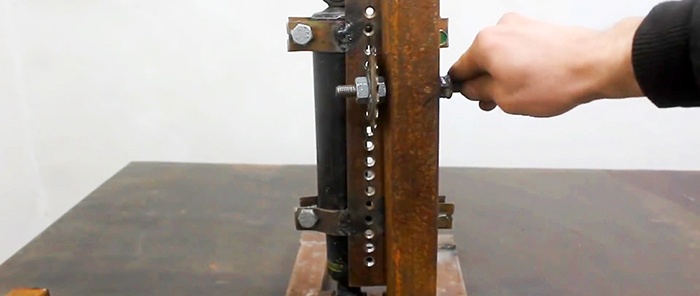
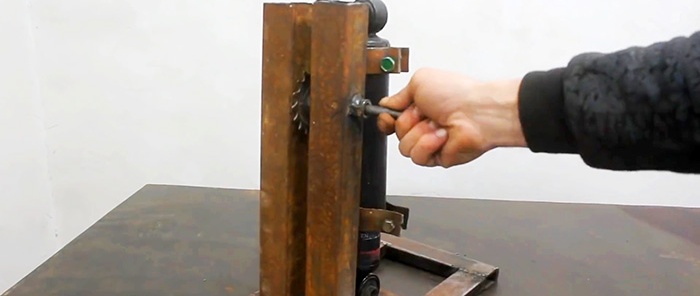
After this, the steering wheel is welded onto the head of the star bolt. To the lower clamps on the shock absorbers you need to weld a clamp on the tube, made to mount the drill body.
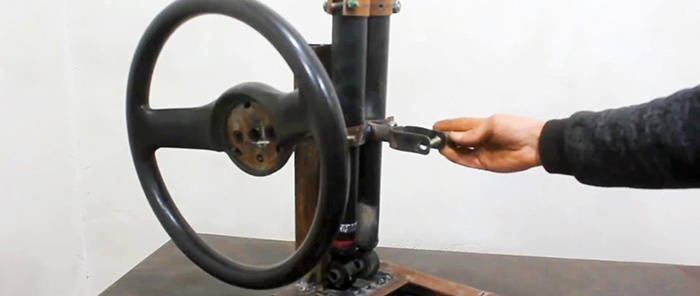
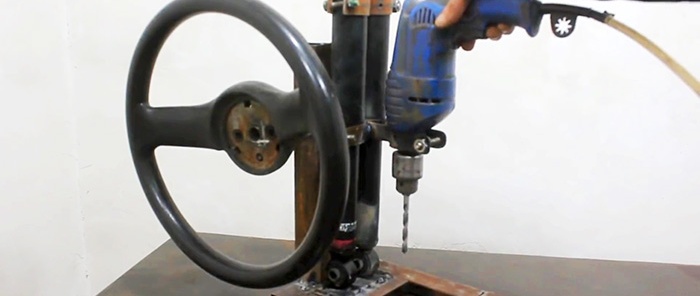
Also, for reliability, you should prepare a large clamp to tighten the shock absorbers with the sprocket stand together.
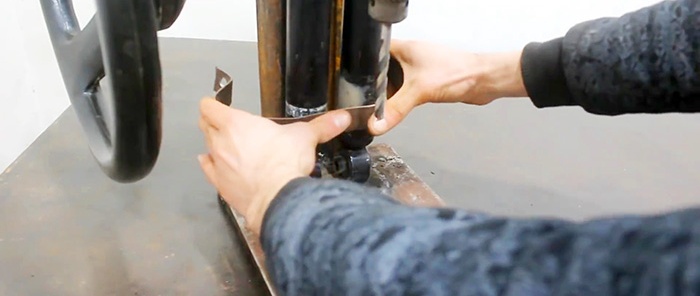
By holding the drill in the stand, you can raise and lower it by rotating the steering wheel. Shock absorbers act as a guide without play, so if the chuck does not dangle, the drilling quality will be close to that of a full-fledged drilling machine.
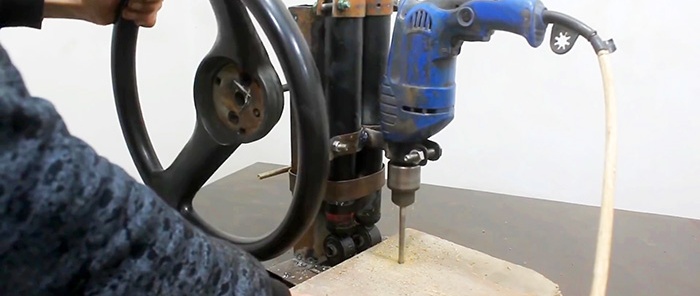
Watch the video
Similar master classes
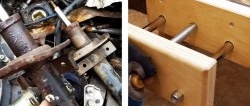
How to make a vice from old shock absorbers
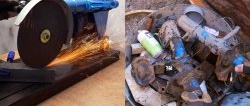
How to make a cutting machine from an angle grinder and old shock absorbers
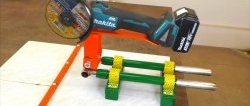
A stand for an angle grinder made from the handle of a children's bicycle. Extremely
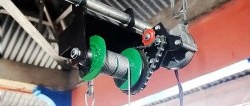
Electric winch made from a car windshield wiper and a bicycle one
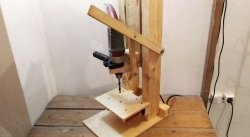
Drill stand two in one: drilling and grinding machine
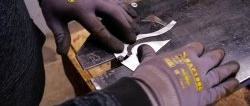
How to make a simple machine for shaped cutting of metal from a drill
Particularly interesting
Comments (1)