The simplest grinder made from an angle grinder, a bicycle hub and a timing roller
A belt sander is often easier to use than regular sandpaper. This is quite large equipment, unsuitable for a cramped workshop. If you lack space for storing a belt sander, you can choose a compromise option - make a grinder attachment for an angle grinder. In terms of functionality, it almost corresponds to a full-size machine, while being much more compact and cheaper.
To assemble the machine bed, you need to take a 40x40 mm profile pipe equal in length to the angle grinder and weld a small section of any sufficiently strong profile 8-10 cm to it in the middle.
A strip of 40x10 mm is welded to the resulting T-shaped blank. It will serve as a stand for tensioning the roller. Its length should be greater than the size of the tape that you plan to use.
To attach the angle grinder to the frame, you need to prepare 2 threaded bolts as used on its standard handle. The profile pipe is drilled from below so that it is possible to attach an angle grinder to it by screwing a bolt into the hole for the handle.
Next, an L-shaped mount on the side is welded from a thin profile pipe. It is also drilled to allow the second mounting bolt to be screwed into the side hole for the handle.
A bicycle wheel hub is installed on the angle grinder shaft. To do this, you need to weld a spare standard nut onto it to clamp the cutting disc or a regular M14.
The bushing will act as a drive roller. The old timing belt tension roller of the car will serve as a slave. To do this, you will need to select and press a bearing into it.
Using a steel strip, you need to make a tension arm for the driven roller. A hole is made in it and in the stand previously welded to the frame to tighten the parts with a bolt.
The drilling distance is selected according to the size of the existing sanding belt. A hole is made at the edge of the shoulder for screwing the driven roller. On the bolt used for this, you can install the required number of nuts and washers to move the extension of the driven roller in line with the drive one.
To tension the tape, you need to install a spring, hooking it to the edge of the shoulder opposite to the roller. To hook from below, you need to weld a small bolt to the rack.
This tool can be used suspended when stripping pipes, or clamped in a vice for more delicate work. Since it uses narrow rollers, a purchased sanding belt can be cut into several narrow rings, which will provide significant savings on abrasive materials.
Materials:
- profile pipes 10x10 mm, 40x40 mm;
- bolts, nuts M6-M16;
- strip 40x10 mm;
- bicycle wheel hub;
- belt tension roller with bearing;
- extension spring;
- sanding belt.
Machine manufacturing process
To assemble the machine bed, you need to take a 40x40 mm profile pipe equal in length to the angle grinder and weld a small section of any sufficiently strong profile 8-10 cm to it in the middle.
A strip of 40x10 mm is welded to the resulting T-shaped blank. It will serve as a stand for tensioning the roller. Its length should be greater than the size of the tape that you plan to use.
To attach the angle grinder to the frame, you need to prepare 2 threaded bolts as used on its standard handle. The profile pipe is drilled from below so that it is possible to attach an angle grinder to it by screwing a bolt into the hole for the handle.
Next, an L-shaped mount on the side is welded from a thin profile pipe. It is also drilled to allow the second mounting bolt to be screwed into the side hole for the handle.
A bicycle wheel hub is installed on the angle grinder shaft. To do this, you need to weld a spare standard nut onto it to clamp the cutting disc or a regular M14.
The bushing will act as a drive roller. The old timing belt tension roller of the car will serve as a slave. To do this, you will need to select and press a bearing into it.
Using a steel strip, you need to make a tension arm for the driven roller. A hole is made in it and in the stand previously welded to the frame to tighten the parts with a bolt.
The drilling distance is selected according to the size of the existing sanding belt. A hole is made at the edge of the shoulder for screwing the driven roller. On the bolt used for this, you can install the required number of nuts and washers to move the extension of the driven roller in line with the drive one.
To tension the tape, you need to install a spring, hooking it to the edge of the shoulder opposite to the roller. To hook from below, you need to weld a small bolt to the rack.
This tool can be used suspended when stripping pipes, or clamped in a vice for more delicate work. Since it uses narrow rollers, a purchased sanding belt can be cut into several narrow rings, which will provide significant savings on abrasive materials.
Watch the video
Similar master classes
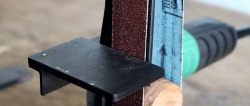
How to make a belt grinder without welding on the base
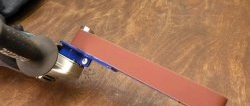
How to make a grinder attachment for an angle grinder
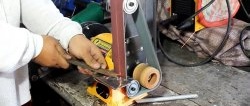
We supplement the emery with a grinder with our own hands
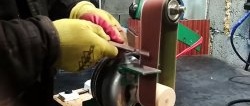
The simplest grinder without a lathe from a washing machine engine
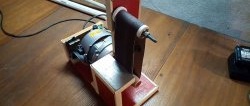
The simplest grinder without welding and turning from a washing machine engine
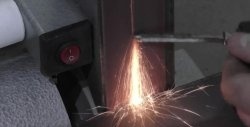
Grinder from a washing machine engine
Particularly interesting
Comments (0)