How to make a useful machine for shape cutting of metal from an old low-power motor
For shaped cutting of roofing materials made of sheet metal and steel sheets, a cricket drill attachment is used. These nibblers cut perfectly, but they are difficult to hold in your hands, so the cutout turns out to be deviated from the markings. To eliminate this drawback of the nozzle, you can make a small, lightweight machine based on it.
You need to make a clamp from plywood to attach the nozzle. To do this, 2 parts are cut out in the form of rings with an eye.
They stick together.
To make the machine body, you need to cut 4 rectangles from plywood.
Their size is selected depending on the dimensions of the engine. On each workpiece, 2 opposite chamfers are cut at 45°. Then the parts are connected in a line with masking tape, the chamfers are smeared with glue, and the blanks are glued into a box. It is additionally fixed in the corners with self-tapping screws.
When the clamp blank is dry, it needs to be sanded. The eyelet is then cut lengthwise into the ring. A hole is drilled in the side to tighten it with an M6 bolt.
A hole is made in the box. You need to match it with the clamp ring, and screw the latter on from the outside.
2 corners are screwed to the engine housing. With them, it should fit tightly inside the box. The motor is screwed so that the shaft faces the center of the hole with the clamp.
A tube bushing is pressed onto the motor shaft. It needs to be fixed. To do this, a hole is drilled in the shaft and bushing, then the pin is driven in.
The bottom for the box is cut out of plywood. It is screwed on and the frame is painted. The power button is embedded on the side. A power cable with a plug is laid through it to the engine.
Nibblers are inserted into the clamp. Their shaft should fit tightly into the bushing. Then the clamp is tightened.
Finally, a plywood tabletop with a cutout for scissors is screwed onto the machine.
The result is a convenient machine for cutting sheet steel. Depending on the parameters of the scissors, it can work with metal with a cross-section of up to 1.2 or 1.8 mm. It also copes well with plastic and thin plywood up to 2 mm.
Materials:
Machine manufacturing process
You need to make a clamp from plywood to attach the nozzle. To do this, 2 parts are cut out in the form of rings with an eye.
They stick together.
To make the machine body, you need to cut 4 rectangles from plywood.
Their size is selected depending on the dimensions of the engine. On each workpiece, 2 opposite chamfers are cut at 45°. Then the parts are connected in a line with masking tape, the chamfers are smeared with glue, and the blanks are glued into a box. It is additionally fixed in the corners with self-tapping screws.
When the clamp blank is dry, it needs to be sanded. The eyelet is then cut lengthwise into the ring. A hole is drilled in the side to tighten it with an M6 bolt.
A hole is made in the box. You need to match it with the clamp ring, and screw the latter on from the outside.
2 corners are screwed to the engine housing. With them, it should fit tightly inside the box. The motor is screwed so that the shaft faces the center of the hole with the clamp.
A tube bushing is pressed onto the motor shaft. It needs to be fixed. To do this, a hole is drilled in the shaft and bushing, then the pin is driven in.
The bottom for the box is cut out of plywood. It is screwed on and the frame is painted. The power button is embedded on the side. A power cable with a plug is laid through it to the engine.
Nibblers are inserted into the clamp. Their shaft should fit tightly into the bushing. Then the clamp is tightened.
Finally, a plywood tabletop with a cutout for scissors is screwed onto the machine.
The result is a convenient machine for cutting sheet steel. Depending on the parameters of the scissors, it can work with metal with a cross-section of up to 1.2 or 1.8 mm. It also copes well with plastic and thin plywood up to 2 mm.
Watch the video
Similar master classes
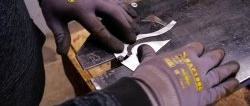
How to make a simple machine for shaped cutting of metal from a drill
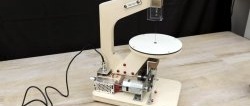
How to assemble a string jigsaw for figure cutting
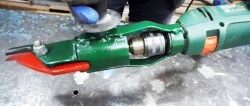
Homemade drill attachment for fast metal cutting
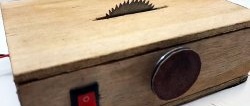
How to make a miniature 2 in 1 circular sharpening machine for
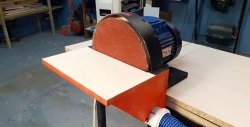
A very simple grinding machine made from available materials
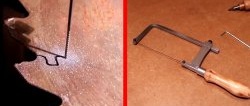
How to make a reliable jigsaw for shape cutting
Particularly interesting
Comments (0)