How to Solder Copper Wire to Aluminum Foil
Anyone with even a little soldering experience knows that solder does not stick well to aluminum. This metal instantly oxidizes, and the formed film interferes with soldering, so it must be literally scraped off, preventing air from accessing the protected area. When it is necessary to solder a wire with a thin foil that breaks at the slightest mechanical friction, you need to act differently.
Usually, all kinds of screens are made from foil in radio electronics, which need to be connected to a common wire.
What you will need:
- Soldering iron;
- solder;
- universal flux DBL-800 from AliExpress - http://alii.pub/64xsle
- cotton wool
I would also like to draw attention to the universal Chinese flux. Which not only easily solders aluminum, but also any other metal, be it stainless steel, brass, regular and galvanized steel, highly oxidized copper, etc.
Therefore, it is extremely necessary to keep such a useful flux in your home workshop.
Aluminum foil soldering process
A drop of flux is poured onto the aluminum foil at the soldering site.
You can immediately notice microbubbles, indicating the reaction is taking place.Then it is soaked with cotton wool so that the surface simply remains wet.
After this, the solder will easily stick to the flux-coated area.
It won't be difficult to connect the wire to it.
The whole secret is simply a good flux, as well as its use without excess. There is no need to solder the foil when there is literally a puddle of flux on it.
When torn off, the foil breaks, in place of the soldering.
Watch the video
Similar master classes
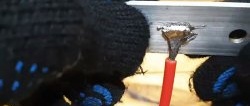
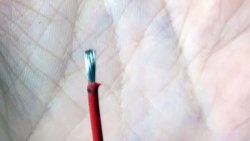
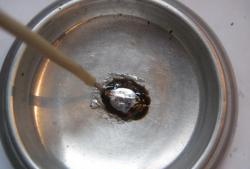
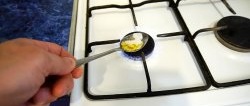
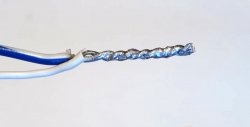
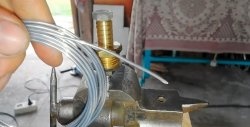