How to make a double bearing housing from available materials
Expensive equipment that few people can afford unless they plan to use it professionally. For amateur use, it is more profitable to make it yourself. Homemade lathes, saws and similar machines use a two-bearing bearing assembly (housing). So that it has minimal runout, it can be made using the proposed method. This is a low-cost, but very worthy solution that is not difficult to repeat at home.
Materials:
- Bearings 50x80 mm – 2 pcs.;
- pipe 50 mm, 70 mm;
- stud M4-M6;
- corner 50x50 mm;
- channel 80-120 mm.
Manufacturing process of double bearing housing
The assembly of a homemade bearing assembly should begin with the manufacture of a housing for the bearings. They are made from scraps of pipe of a smaller diameter, in this case 70 mm. In width they should be approximately 8-10 mm wider than the bearing. The resulting rings are cut lengthwise and stretched.
Each workpiece is placed on a bearing and then compressed with a vice.
Then the remaining gap in the body is welded with an insert cut from another section of pipe. The seam is cleaned.
The body is scalded on one side to create an internal rim. It should prevent the bearing from passing through.
The bearings are pressed all the way into the housing blanks.
Then you need to make removable sides on the other side. To do this, narrow insert rings are made from a pipe in a similar way.
The rings are pressed into the housing close to the bearing race. To attach them, you need to drill them together with the holder in three places, and cut M4-M6 threads in the holes. Sections of a pin are screwed into them and slots are cut into them for a screwdriver. This way, it will be possible to remove the rings to replace the bearings if necessary.
Now we need to work on the assembly frame. It can be made from a section of channel. Along its width, 2 blanks are cut from the corner. It is to them that the housings with bearings will be welded. The corners and channel are drilled along the edges and threads are cut into them. The upper edge of the corners needs to be cut off in a semicircle, forming a concavity for welding the bodies.
Housings with bearings must be welded to the corners. A pipe spindle is inserted into the latter, and they are screwed to the frame.
Thus, we get a powerful double-bearing bearing housing that does not bend under load. Its bearings are replaceable, making the machine easier to maintain in the future.
Watch the video
Similar master classes
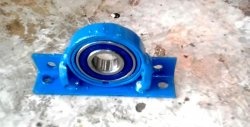
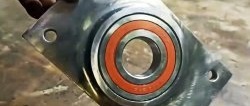
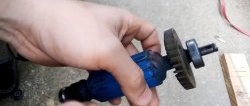

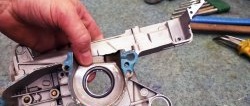
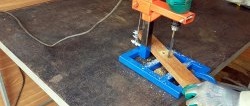