How to weld pipes of different diameters evenly
If you need to reliably and hermetically weld pipes of different diameters, you can use the old proven method by narrowing the end of the larger one. The resulting connection will not only be reliable, but also beautiful.
The edges of the pipes to be welded must be trimmed evenly.
After this, it is necessary to divide the circumference of the larger one into 8 equal parts. It is convenient to do this by drawing a circle of this diameter on paper and transferring the markings from it to the pipe.
A circle is drawn 10 cm from the edge of the marked pipe.
After this, you need to divide this part into 8 strips based on the marks.
Next, you need to draw wedges, cutting which you can narrow the edge to the diameter of a smaller pipe. To do this, you need to make a calculation using the formula (d1-d2)/8.
The resulting value is divided in half. From each longitudinal strip you need to step back to the left and right by the given distance and put marks.
Oblique lines are drawn along them, after which wedges are cut out.
Now, by wrapping the edges of the cut pipe with a stretched rubber band, you can evenly compress it to the required diameter.
The pipes are then joined and welded.
Longitudinal cuts are also welded. After sanding the seams, the connection will look like a factory one.
What you will need:
- welding machine;
- Bulgarian;
- rubber band;
- ruler;
- marker;
- paper;
- compass.
Pipe welding process
The edges of the pipes to be welded must be trimmed evenly.
After this, it is necessary to divide the circumference of the larger one into 8 equal parts. It is convenient to do this by drawing a circle of this diameter on paper and transferring the markings from it to the pipe.
A circle is drawn 10 cm from the edge of the marked pipe.
After this, you need to divide this part into 8 strips based on the marks.
Next, you need to draw wedges, cutting which you can narrow the edge to the diameter of a smaller pipe. To do this, you need to make a calculation using the formula (d1-d2)/8.
The resulting value is divided in half. From each longitudinal strip you need to step back to the left and right by the given distance and put marks.
Oblique lines are drawn along them, after which wedges are cut out.
Now, by wrapping the edges of the cut pipe with a stretched rubber band, you can evenly compress it to the required diameter.
The pipes are then joined and welded.
Longitudinal cuts are also welded. After sanding the seams, the connection will look like a factory one.
Watch the video
Similar master classes
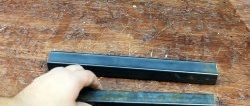
Reliable connection of profile pipes without welding or bolts
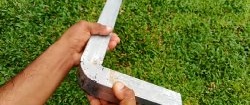
Unusual corner connection of a profile pipe
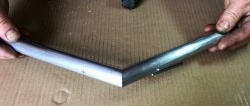
How to connect tubes at any angle without welding
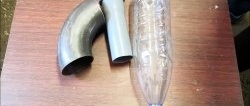
We connect 2 pipes of different diameters with a PET bottle
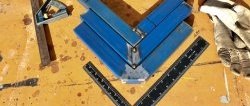
3 ways to weld a profile at right angles
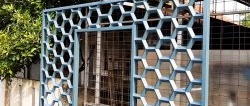
How to weld a beautiful honeycomb partition from a square one
Particularly interesting
Comments (0)